Chargenrückverfolgung bei der Muelhens GmbH
Die Chargenrückverfolgung zur Gewährleistung einer lückenlosen Dokumentation der Herstellung und Distribution der Produkte bekommt nicht mehr nur in der Pharma- und Lebensmittelindustrie, sondern auch zunehmend in anderen Industriesektoren einen hohen Stellenwert zugesprochen. Bei Muelhens untersuchte man die gegebenen Strukturen, Funktionen und Prozesse um eine effiziente und in allen Prozessschritten transparente Chargenrückverfolgung einzuführen.
Inhaltsverzeichnis
1. Das Unternehmen2. Chargenrückverfolgung bei der Muelhens GmbH
Projektstruktur, Geschäftssicht, Codierung, Prozesssicht, Anwendungssicht, Lagerverwaltungssystem, Chargenidentifikation
3. Implementierung
Redesign der Prozesse
4. Erfahrungen aus der Praxis
Investitionen
5. Erfolgsfaktoren
1. Das Unternehmen
Cosmopolitan Cosmetics ist der Marktführer für Duft- und Kosmetikstoffe in Deutschland.
Unter Cosmopolitan Cosmetics sind seit Oktober 1997 alle Duft- und Kosmetik-Aktivitäten der Wella-Gruppe zusammengefasst. Dazu gehören insbesondere die MUELHENS GMBH (Köln), die PARFUMS ROCHAS S.A. (Poissy), GUCCI PARFUMS sowie eigene Tochtergesellschaften und Regionalbüros. COSMOPOLITAN COSMETICS ist in über 150 Ländern weltweit vertreten. Die wichtigsten Produktionsstandorte von COSMOPOLITAN COSMETICS sind Köln-Bickendorf und Poissy (Frankreich). Am Standort Köln-Bickendorf ist der Bereich OPERATIONS INTERNATIONAL angesiedelt, zu dem insbesondere die Funktionen F&E, Planung, Einkauf, Produktion, Logistik sowie das Technik Center gehören.
Hohe Ansprüche an die Qualität der Marken, professionelle Kommunikation und Verkaufsförderung sowie eine konsequent umgesetzte Vermarktungspolitik zeichnen diese Organisation aus.
Durch eine Angliederung des Unternehmens an Procter & Gamble (P&G) wurde Cosmopolitan Cosmetics vor die Aufgabe gestellt, sich an die Prozesse und Standards des Gesamtkonzerns anzupassen.
Das in den nachfolgenden Kapiteln beschriebene Projekt „Chargenrückverfolgbarkeit“ wurde am Standort Köln-Bickendorf bei der Muelhens GMBH, einer Vertriebstochter der Cosmopolitan-Cosmentics-Gruppe durchgeführt.
Hintergrund
Der Name Muelhens ist untrennbar verbunden mit dem weltweit berühmten Parfum „4711 Echt Kölnisch Wasser“, dessen Rezeptur Wilhelm Muehlens vor über 200 Jahren als Hochzeitsgeschenk erhielt. Der Grundstein für das Unternehmen wurde somit 1792 gelegt. Seitdem ist dieses Eau de Cologne Synonym für erfolgreiche Markenführung in der Kosmetik- und Duftbranche.
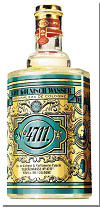
Branche, Produkte und Zielgruppen
Die Duft- und Kosmetik-Produkte von Cosmopolitan Cosmetics sind in allen Preissegmenten vertreten. So kommen Duftwässerchen für den Alltag ebenso wie auch edle Parfums aus der selben „Schmiede“.
Damit ist auch die Zielgruppe sehr breit gefächert. Von trendorientierten Mode- und Lifestyleprodukten für die junge Generation über Personality-Düfte für die erfolgreiche Frau oder den erfolgreichen Mann bis hin zu traditionsbewussten Käuferschichten ist Cosmopolitan Cosmetics sowohl im Produkte- als auch im Zielgruppenbereich breit vertreten. Das Produktsortiment umfasst unter anderem die Marken: 4711 - Mexx - Bruno Banani - Escada - Bogner Mont Blanc - Yardley - Puma - Cindy Crawford - Gabriela Sabatini - Naomi Campbell - Irish Moos.
Partner im Projekt Chargenrückverfolgung
OTB
Die OTB AG aus Basel (CH) ist ein Unternehmen für Industrieplanung und Beratung. OTB ist spezialisiert auf die integrale und parallele Planung und Realisierung von organisatorischen, technischen und baulichen Massnahmen bei Projekten aus der Industrie.
Im Projekt Chargenrückverfolgung erarbeitete OTB gemeinsam mit dem Muelhens-Projektteam das Konzept und war Gesamtkoordinator in der Realisierung.
Logisys
Die Firma Logisys aus Ulmen (D) ist Spezialist für Lagerverwaltungssysteme (LVS). In den Bereichen Gross- und Feinkommissionierung bei Muelhens ist das Lagerverwaltungssystem von Logisys im Einsatz. Im Rahmen des Projektes Chargenrückverfolgung bestand für Logisys die Aufgabe, die konzeptionell erarbeiteten Erweiterungen für das LVS zu realisieren.
2. Chargenrückverfolgung bei der Muelhens GmbH
Die Chargenrückverfolgung zur Gewährleistung einer lückenlosen Dokumentation der Herstellung und Distribution der Produkte bekommt nicht mehr nur in der Pharma- und Lebensmittelindustrie, sondern auch zunehmend in anderen Industriesektoren einen hohen Stellenwert zugesprochen.
Dabei geht es in erster Linie um den Verbraucherschutz und die Transparenz gegenüber dem Kunden. Ein nicht minder wichtiger Aspekt ist der Schutz des Unternehmens vor möglichen Schadenersatzansprüchen aufgrund von Mängeln oder durch die Produkte verursachter Schäden. Ein Fehler im Produkt muss nicht zwangsläufig bedeuten, dass der Hersteller selbst der Verursacher ist. Der Mangel kann irgendwo in der Supply Chain entstanden sein. Klagen mit astronomisch hohen Forderungen, die immer wieder in den Medien publiziert werden, treiben viele Unternehmen dazu, ihre Vorbeugemassnahmen zu erweitern. Dazu gehört ein durchgängiges Reportingsystem, das Aufklärung durch eine lückenlose Dokumentation der Prozesse ermöglicht.
Auch bei Muelhens war dies einer der Gründe, die gegebenen Strukturen, Funktionen und Prozesse zu untersuchen und eine effiziente und in allen Prozessschritten transparente Chargenrückverfolgung einzuführen. In einem ersten Schritt sollte der Standort Köln untersucht, ein Konzept entwickelt und dieses realisiert werden. In einem zweiten Schritt sind alle anderen Standorte von Cosmopolitan Cosmetics zu integrieren.
Bei der Konzeption mussten alle Bereiche (Produktion, Logistik, Qualitätssicherung und Informatik) mit ihren relevanten Prozessen berücksichtigt werden. Dies waren im Einzelnen:
1) Produktion
- Wareneingang Rohmaterial
- Herstellung von Füllgut
- Abfüllung und Konfektionierung von Halbfertig- und Fertigwaren
2) Externe Produktion
- Herstellung, Abfüllung und Konfektionierung
- Dokumentation der von Muelhens bereitgestellten Chargen und Mengen
3) Lagerung
- Wareneingang von Halbfertig- und Fertigwaren von Fremdfertigern
- Lagerung und Verwaltung von Halbfertig- und Fertigwaren im Haus oder bei einem externen Dienstleister
- Warenausgang von Halbfertig- und Fertigwaren zu Fremdfertigern
- Nachschub in die Kommissionierung
4) Kommissionierung
- Kundenspezifische Grosskommissionierung = kleinste kommissionierte Einheit ist der Originalkarton
- Kundenspezifische Feinkommissionierung = kleinste kommissionierte Einheit ist das Einzelstück
5) Versand
- Versand von kommissionierter Ware an den Kunden
6) Retourenhandling
- Nacharbeit
- Wiedereingliederung der Waren in die Prozesse
7) Qualitätssicherung
- In-Prozess-Kontrolle (laufende Qualitätskontrolle während der Prozessfertigung)
- Musterzug bei Wareneingang
- Prüflosverwaltung
Die nachfolgende Abbildung 1 zeigt die Projektstruktur:
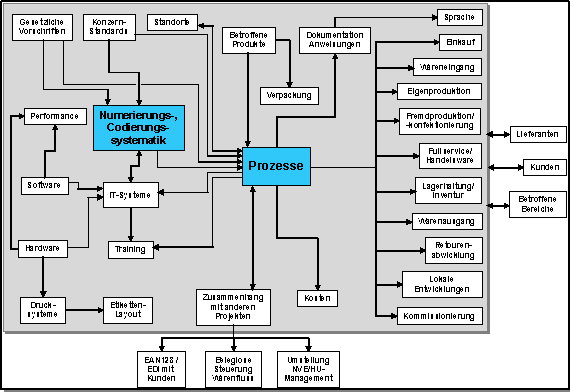
Abbildung 1: Projektstruktur Chargenrückverfolgung Fertigware
Geschäftssicht
Mit der Einführung einer Chargenrückverfolgung verfolgte Muelhens analog den Standards von Procter & Gamble das Ziel einer bestmöglichen Qualitätssicherung und einer lückenlosen Dokumentation aller Vorgänge und Produkteigenschaften. Zudem reduziert Chargenrückverfolgung das Schadensrisiko, das mit dem Szenario eines Produkterückrufs verbunden ist: Durch die Verfolgung und Identifikation der betroffenen Charge auch im Distributionskanal könnte ein Rückzug gezielter und möglicherweise eindeutig vor Produktausgabe an Endverbraucher geschehen, was einen viel geringeren Produkt- und Imageschaden nach sich ziehen würde.
Voraussetzung für eine durchgängige Chargenrückverfolgung, aber auch für werksübergreifende Synergien in der Logistik, sind konzernweite Standards zur Codierung der Chargen und Etikettierung der Gebinde. Diese werden nachfolgend vorgestellt.
Codierung der Chargen
Die Ausgangssituation zeigte eine länderspezifische heterogene Chargenauszeichnung und –verwaltung. An den einzelnen Standorten kommen verschiedene Informationssysteme zum Einsatz, deren Funktionalität der Chargenverwaltung stark differiert.
Das Ziel für die Auszeichnung der Waren bestand darin - beginnend mit dem Füllgut, über die Halbfertigware bis zur Fertigware - den gegebenen Standard von Procter & Gamble zu übernehmen, um eine einheitliche Codierungssystematik zu erzielen.
So gilt neu für das Füllgut folgende Chargennomenklatur:
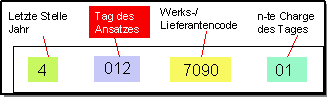
Da zwischen der Herstellung des Füllgutes und der eigentlichen Abfüllung in Flaschen, Tuben oder andere Primärverpackungen – bedingt durch die Reifezeit von alkoholischen Füllgütern – mehrere Wochen liegen, wird in der Chargennummer der abgefüllten Ware der effektive Tag der Abfüllung codiert.
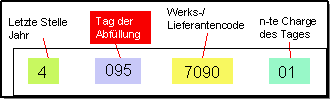
Da bei Muelhens und deren Fremdfertigern aber nicht nur Einzelprodukte hergestellt werden, sondern auch Geschenkpackungen oder Displays* mit Kombinationen aus mehreren Produkten erstellt werden, musste dieser Artikelgruppe ebenfalls Rechnung getragen werden. [* Geschenkpackungen und Displays bestehen aus mehreren chargenpflichtigen Artikeln. Somit muss der Tag der Produktion (Produktzusammenstellung) codiert werden].
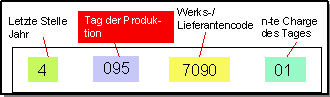
Prozesssicht
Die nachfolgende Abbildung zeigt das Business Szenario, in dem die einzelnen Prozessstufen aufgezeigt sind.
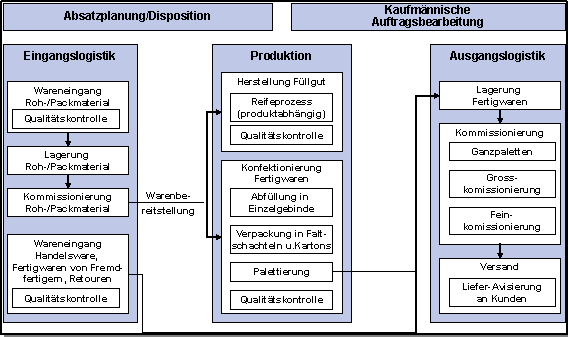
Abbildung 2: Gesamtprozess inkl. Chargenänderung und -generierung
Für eine Chargenrückverfolgung ist es erforderlich, jede Chargenänderung und -Neugenerierung über die verschiedenen Prozesse (Eingangslogistik – Produktion – Ausgangslogistik) genau und vor allem eindeutig zu dokumentieren, damit im Bedarfsfall ersichtlich ist, welches Rohmaterial in welches Füllgut oder welches Füllgut in welcher Fertigware verwendet wurde. Es muss zum einen möglich sein, die Prozesskette rückwärts zum Lieferanten - d.h. zum Wareneingang - zu verfolgen. Gleichwohl ist es notwendig auch in Richtung der Vertriebswege - also zum Versand - der Ware eine durchgängige Chargendokumentation zu pflegen, damit ersichtlich ist, welche Fertigwarenchargen an welchen Kunden versendet werden.
Dafür stehen in den einzelnen Prozessstufen verschiedene Datenmanagementsysteme zur Verfügung. Es galt, diese Systeme um entsprechende Funktionalitäten zur Chargendokumentation zu erweitern und vor allem aufeinander abzustimmen, damit der physische Warenfluss mit dem dazugehörigen Informationsfluss synchron verläuft.
So sind beispielsweise alle Wareneingänge, die Herstellung von Füllgut sowie das Auftragsmanagement der Produktion in SAP abgebildet. Notwendige Informationen für die Konfektionierung der Fertigwaren werden zum einen über die Zentrale Betriebsdatenerfassung, zum anderen über eine Etikettiersoftware bereitgestellt. Die bestehende Etikettiersoftware war jedoch relativ alt und besass keinerlei Schnittstellen zu anderen Informationssystemen, sodass Muelhens parallel zum Projekt der Chargenrückverfolgung eine Pilotlinie mit einer neuen Produktions- und Etikettiersoftware (PESO) implementierte. Diese neue Software hat die Möglichkeit, die Chargenvergabe an den Linien zu steuern, Auftrags- und Gebindedaten zu verknüpfen und dann an SAP zur Lieferavisierung zu übermitteln. Die stellplatzbezogene Lagerverwaltung im Fertigwarenlager erfolgt wiederum in SAP.
Kundenaufträge, für die eine auftragsspezifische Kommissionierung notwendig ist, werden in den beiden Bereichen Gross- und Feinkommissionierung bearbeitet. In der Grosskommissionierung findet eine Kommissionierung auf Originalkartonebene statt. Das heisst, die Kartons bleiben artikel- und chargenrein. Aufträge der Feinkommissionierung enthalten mehrere Artikel und damit auch mehrere Chargen in einem Karton. Die Materialien dafür werden in einem separaten Lagerverwaltungssystem verwaltet. Dabei war es notwendig, die erforderlichen Nachschubinformationen aus dem Zentrallager (aus SAP), die an das LVS gesendet werden, zu erweitern, um die Chargeninformation in allen DV-Systemen präsent zu haben.
Die für den Versand notwendige Warenausgangsbuchung erfolgt wiederum in SAP, sodass entsprechende Kommissionierrückmeldungen vom LVS an SAP über eine Schnittstelle zurückgeschickt werden müssen.
Auch bei externer Produktion bei Fremdfertigern, werden die Bestände, welche den Fremdfertigern zur Fertigung zugestellt wurden inklusive Chargeninformation in SAP verwaltet und dokumentiert.
Die Qualitätskontrolle verfügt über ein separates Labor-Informations-Management-System (LIMS), das alle Prüfergebnisse zu einer Charge dokumentiert.
Anwendungssicht
Nachfolgende Grafik zeigt die EDV-Landschaft in Bezug auf die einzelnen Produktions- und Logistikprozesse.
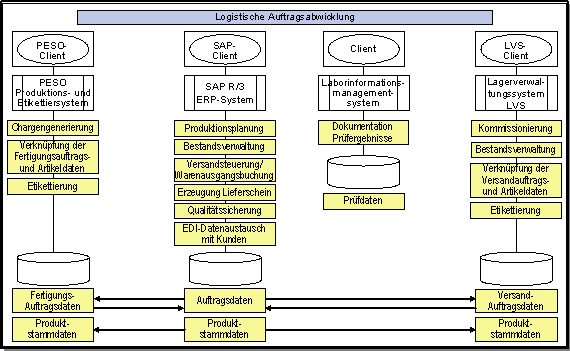
Abbildung 3: Systemlandschaft bei der Muelhens GmbH
Systemübersicht
SAP
Für die logistische Auftragsabwicklung bei der Muelhens AG ist SAP R/3 das federführende System, in dem die Verwaltung der Stamm- und Auftragsdaten sowie die Produktionsplanung stattfinden. Weiterhin ist SAP im Einsatz für die Verwaltung der Materialbestände, für die Produktion und das Fertigwarenlager sowie für die Generierung von Prüflosen zur Qualitätssicherung. Über Schnittstellen werden alle relevanten Daten in die einzelnen Subsysteme (PESO, LVS) übertragen.
PESO (Produktions- und Etikettier-Software)
Im Bereich der Produktion (Konfektionierung der Fertigwaren) werden alle Auftragsdaten von SAP via Schnittstelle an das Subsystem PESO übermittelt. In PESO erfolgt anhand der definierten Chargennomenklatur (siehe Codierung der Chargen) die Vergabe der Chargennummer sowie die Etikettierung der Ware. Weiterhin werden alle fertigungsauftrags- und artikelrelevanten Informationen systematisch miteinander verknüpft und an SAP zurückgemeldet. Folgende Informationen werden miteinander kombiniert und an SAP elektronisch übermittelt:
- Auftragsnummer Fertigungsauftrag
- Artikelnummer
- Chargennummer
- Menge
- Graumarktcode (bei graumarktpflichtigen Artikeln)
- SSCC der Kartons und Paletten (SSCC = Serial Shipping Container Code, eine eindeutige Identifikation für Fördermittel)
Durch Anscannen des Paletten-SSCCs kann ein Wareneingang schnell gebucht werden. Durch die Verknüpfung der Daten sind alle notwendigen Informationen im SAP vorhanden.
LVS (Lagerverwaltungssystem)
Das LVS erhält die kundenspezifischen Auftragsdaten von SAP. In den beiden Kommissionierbereichen Gross- und Feinkommissionierung werden sämtliche Bestände mit den in SAP vorhandenen Informationen (Artikel, Charge, Menge, SSCC) verwaltet. Der Kommissionierprozess ist im Subsystem LVS abgebildet. Handelt es sich bei dem Versandauftrag um Ganzpaletten, erfolgt eine Durchschleusung der Ware durch die Kommissionierung. Muss eine Mischpalette oder im Fall der Feinkommissionierung ein Karton mit unterschiedlichen Artikeln und Chargen erstellt werden, so findet eine Neuetikettierung der Gebinde im LVS statt.
Nach Abschluss des Kundenauftrages erfolgt eine Rückmeldung der Versandauftragsdaten an SAP, so dass die Warenausgangsbuchung erfolgen und der Versand eingeleitet werden kann. Folgende Informationen – relevant für die Chargenrückverfolgung – werden zurückgemeldet:
- Liefernummer (damit ist der Kunde ersichtlich)
- Artikelnummer
- Chargennummer
- Menge
- Graumarktcode (bei graumarktpflichtigen Artikeln)
- SSCC der Kartons und Paletten
Mit den einzelnen SSCCs sind unter anderem die Artikel- und die Chargennummer verknüpft, sodass diese Informationen durch einmaliges Anscannen des SSCCs verfügbar werden.
LIMS (Labor-Informations-Management-System)
Die Generierung eines Prüfloses wird durch SAP automatisch angestossen. Dies erfolgt sowohl bei Wareneingängen von Roh- und Packmaterial, als auch bei Anlieferungen von Handelsware, Fertigware von Fremdfertigern und Retouren.
Die Dokumentation der Prüfergebnisse erfolgt in einem separaten LIMS.
Neue Etiketten zur schnellen Chargenidentifikation
Um die schnelle Identifikation der Charge zu gewährleisten, wurden die Etiketten entsprechend angepasst, sodass die Chargennummer neu maschinenlesbar codiert wurde.
Das nachfolgende Beispiel zeigt ein altes und ein neues Etikett für einen Originalkarton.
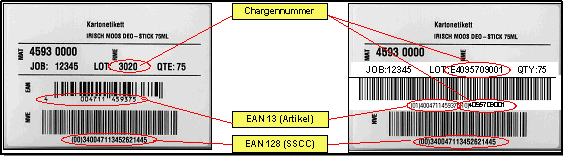
Abbildung 4: Vergleich altes (links) und neues Etikett für einen Originalkarton (Artikel- und Chargenrein)
Auf dem alten Etikett war die Chargennummer lediglich in Klarschrift vorhanden und nur sehr aufwendig zu identifizieren (z.B. manuelle Eingabe in ein EDV-System bei der Kommissionierung).
Aus Sicht der Anwender bestand die Notwendigkeit, die hohen Anforderungen, die an eine Chargenrückverfolgung gestellt werden, möglichst einfach umzusetzen. Die Anwender haben mit den Neuerungen eine grössere Verantwortung, was die Dokumentation von Informationen angeht. Wurde bis dato auf die Erfassung einer Charge in der Kommissionierung verzichtet, müssen die Mitarbeiter jetzt bei jedem Pick nicht nur den Artikel sondern auch die Charge der Palette oder des Kartons erfassen. Damit dafür keine zusätzlichen Scannvorgänge notwendig sind, wurde ein kombinierter Barcode EAN128, bestehend aus der Artikelidentifikation und der Chargennummer, eingeführt, wo beide Informationen in einem Scannvorgang erfasst werden können. Durch PESO wird der gesamte Ablauf der Datenerfassung in der produktionsnachgelagerten Logistik noch mehr vereinfacht, indem dem SSCC auf Karton- oder Palettenetikett sämtliche relevante Informationen wie Artikel, Menge, Charge, Auftrag, Graumarktcode, etc. zugeordnet werden, und mit Identifikation dieses einen Barcodes alle notwendigen Daten erfasst werden.
Untenstehende Bedienermaske zeigt die Informationen, die durch PESO an den Abfülllinien verknüpft werden und an SAP palettenbezogen übermittelt werden.
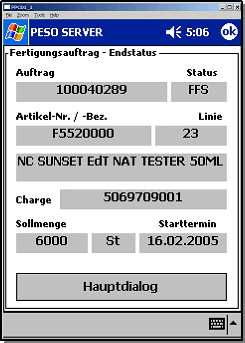
Abbildung 5: Bedienermaske Funkterminal aus dem PESO-Projekt
Verknüpfung von Chargeninformationen
Um im Bedarfsfall schnell die notwendigen Informationen zu einer defekten Charge im System zu finden, wurde auch für die Qualitätssicherung eine zusätzliche Applikation programmiert, in der die Verknüpfung der abgefüllten Chargen zu den bereitgestellten Füllgütern und dem jeweiligen Abfüllauftrag auf einen Blick ersichtlich ist. Nachfolgende Abbildung zeigt die Testversion.
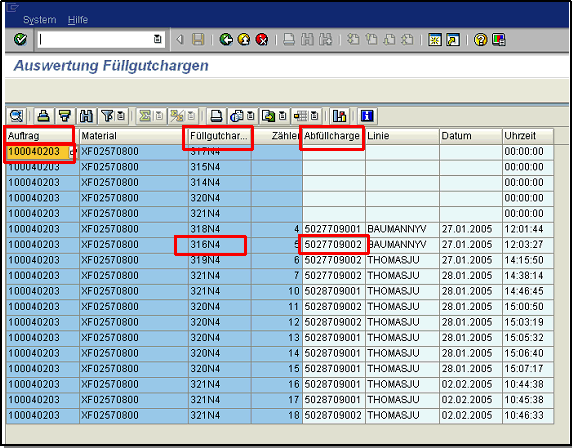
Abbildung 6: Verknüpfungstabelle Füllgutchargen - Abfüllchargen
3. Implementierung
Das Projekt „Chargenrückverfolgbarkeit von Fertigwaren“ war ein abteilungs- und bereichsübergreifendes Projekt. Das Projektteam bestand darum aus Schlüsselpersonen der Fachbereiche Produktion, Logistik, IT, Qualitätssicherung und Strategischer Planung. Die Konzepterarbeitung und Gesamtkoordination für die Realisierung erfolgte durch das Beratungsunternehmen OTB AG aus Basel, die bei Muelhens Projekte im Bereich Logistik und Organisation begleitet.
Die Realisierung der Softwareanpassungen wurde zum einen durch eine Fachabteilung der internen IT und zum anderen durch den Lieferanten des Lagerverwaltungssystems, die Firma Logisys aus Ulmen, ausgeführt.
In einem eng gesteckten Terminplan wurde mit den ersten Anpassungen und Tests auf Seiten SAP Ende 2004 begonnen. Parallel dazu fand die Pflichtenhefterstellung für die Anpassung des Lagerverwaltungssystems statt, um diese Änderungen ab Januar 2005 einführen zu können. Alle Artikel, die der Chargenrückverfolgung unterliegen, sollen ab Juli 2005 chargenpflichtig geschaltet sein.
Projektmanagement und Redesign der Prozesse
Dadurch, dass alle produktiven Bereiche von Muelhens in diesem Projekt involviert waren, kam dem Projektmanagement und der Gesamtkoordination ein hoher Stellenwert zu. Darum wurde OTB als externer Planer beauftragt, die Gesamtkoordination auf einer neutralen Ebene zu übernehmen. Weiterhin bestand die Aufgabe, angrenzende Projekte und Themenfelder (Etikettiersystem, belegloser Waren- und Informationsfluss, elektronische Lieferavisierung etc.) immer im Auge zu behalten und mögliche Synergien zu nutzen.
Die bestehenden Prozesse wurden bereichsübergreifend synchronisiert, um einen durchgehenden Datenfluss ohne Informationsverluste zu gewährleisten.
Softwarelösung
Als erstes wurden die bestehenden Funktionalitäten in den beiden grossen Systemen SAP und Lagerverwaltungssystem erfasst und um die notwendigen Masken, Tabellen und Abfragen für eine Chargenrückverfolgbarkeit erweitert.
Um einen durchgängigen Chargenverwendungsnachweis zu erzielen mussten auch die Fremdfertiger einbezogen werden. Diese verfügen nicht alle über den gleichen hohen EDV-Standard wie Muelhens, weshalb eine einfache Lösung gefunden werden musste. Die Fremdfertiger haben nun mit jedem Auftrag eine Excel-Tabelle auszufüllen, in der die Verwendung der bereitgestellten Chargen eindeutig dokumentiert ist. Diese Informationen werden am Wareneingang im Zentrallager von Muelhens wieder in das SAP erfasst und sind somit durchgängig verfügbar.
4. Erfahrungen aus der Praxis
Anwendung und Unterhalt
Es wäre falsch zu behaupten, die Chargenrückverfolgung habe keine Auswirkungen auf die Arbeitsabläufe der einzelnen Mitarbeiter. Jeder Anwender trägt jetzt eine höhere Verantwortung. Sie besteht in einer genauen Umsetzung jeder einzelnen Arbeitsanweisung sowie in der exakten Erfassung aller Tätigkeiten und Kennziffern. So leistet jeder Mitarbeiter seinen Beitrag für eine saubere Dokumentation des Herstellprozesses.
So weit als möglich wurde versucht, den Spagat zwischen höheren Anforderungen und effizienteren Prozessen durch eine bedienerfreundliche und vor allem eindeutige Gestaltung von Masken und Menüs umzusetzen. Auch der verstärkte Einsatz von EDV-Systemen und Datenvorgaben durch das System erleichtern dem Mitarbeiter die Arbeit.
Investitionen
Der Gesamtaufwand von ca. 280 Manntagen (ohne PESO-Etikettiersystem) gliederte sich in folgende Positionen:
- 55% Beratung, Projektmanagement und Schulungen
- 40% Softwareentwicklung und Tests
- 5% Hardware und Infrastrukturinvestitionen
Zielerreichung
Durch die Erweiterung bestehender Systeme (SAP, Lagerverwaltungssystem) und die Einführung des neuen Etikettiersystems (PESO) wurde eine durchgängige Chargenrückverfolgbarkeit ermöglicht. Eine zukünftige Erweiterung ist durch die Verwendung von Standardmodulen jederzeit möglich.
Da der Erfolg auch von der genauen Dokumentation durch die Mitarbeitenden abhängt, wurden alle Bereiche ausführlich geschult und vor allem auch für die neue Situation sensibilisiert.
5. Erfolgsfaktoren
Erfolgsfaktoren des Projektes waren unter anderem:
- Die Aufnahme der Ist-Situation für alle Bereiche
- Die Vorstellung des Projektes an alle Involvierten. Regelmässige Information an alle Betroffenen und Treffen wichtiger Entscheide im Projektteam
- Die Erarbeitung des Konzeptes in engster Zusammenarbeit mit den Schlüsselpersonen im Projektteam
- Detaillierte Ausschreibung und intensive Pflichtenheft- und Testphase
- Striktes Projektmanagement und zentrale Koordination der einzelnen Realisierungsschritte
Spezialitäten der Lösung
- Das Konzept basiert auf der Nutzung bereits bestehender Systeme und der Synergien aus parallel laufenden Projekten.
- Der Datenerfassung und der Datendurchgängigkeit wurden eine hohe Bedeutung beigemessen.
- Der Zeitrahmen für die Einführung am Standort Köln war eng gesteckt (1/2 Jahr)
- Das Konzept ist mit kleinen Modifikationen aufgrund anderer Softwaresysteme auch an anderen Standorten umsetzbar.
Lessons Learned
Wie in allen Projekten dieser Grössenordnung ist es entscheidend, schon in der Konzeptphase alle betroffenen Bereiche zu integrieren. Denn nur dadurch können entsprechende Erfahrungen eingearbeitet und die flächendeckende Akzeptanz gewährleistet werden.
Parallel dazu müssen die bestehenden Ängste vor der Veränderung abgebaut und die Notwendigkeit der Neuerung allen Beteiligten aufgezeigt werden. Dies bedingt vor allem eine intensive Schulung der Mitarbeiter.
Die notwendige Prozessorientierung und bereichsübergreifende Tragweite einer Chargenrückverfolgung muss allen Beteiligten klargemacht werden, eine Sichtweise „über den eigenen Tellerrand hinaus“ ist zwingend notwendig.
Auf Seiten der Projektleitung zeigte sich ebenfalls, dass so ein Projekt nur gemeinsam bewerkstelligt werden kann und ein striktes Projektmanagement bzgl. Termineinhaltung, Aufgabenerfüllung und Koordination sowohl zwischen internen Abteilungen und Bereichen als auch zwischen Lieferanten und Muelhens unabdingbar ist. Aus diesem Grund war der Aufwand für die planerische Konzeption sowie die Gesamtkoordination und -betreuung auch mit ca. 160 Manntagen von gesamthaft etwa 280 Manntagen der grösste Posten des Projektaufwands.