Otto Fischer AG: Papierloser Warenfluss durch den Einsatz mobiler Datenerfassungsgeräte
Die Otto Fischer AG vertreibt elektrotechnische Produkte an professionelle Elektroinstallateure. Der Kommissionierung fällt in diesem Geschäft eine strategische Bedeutung zu.
Mit dem Einsatz von mobilen Datenerfassungsgeräten konnte das Unternehmen seine Produktivität und Flexibilität erhöhen. Voraus ging ein Projekt, das die Aufnahme und Anpassung der internen Prozesse erforderte. Das Resultat ist ein papierloser Warenfluss von der Kundenbestellung bis zur Warenauslieferung an den Kunden. Die Fallstudie beleuchtet Hintergründe und Erfahrungen dieser Systemeinführung, wobei für den Bereich Kommissionierung detailliert auf Einzelheiten eingegangen wird.
1. Das Unternehmen
Hintergrund, Branche, Produkt und Zielgruppe
Die Otto Fischer AG (OFAG) in Zürich ist der zweitgrösste Elektromaterialgrosshändler der Schweiz. Das 1899 gegründete Familienunternehmen beschäftigt heute rund 280 Mitarbeitende. Mit einem Sortiment von über 250'000 Artikeln, wovon 35'000 an Lager geführt werden, zeichnet sich das Unternehmen als fachkundiger Dienstleister aus.
Zu den Hauptherausforderungen gehört der Preiskampf und Preisdruck in einem stabilen Markt mit konsolidierten Marktteilnehmern. Mit ca. 3'000 Artikel generiert Otto Fischer ca. 80 % des Umsatzes. Um als Vollsortimenter im Markt erfolgreich bestehen zu können, muss die gesamte Sortimentsbreite angeboten werden können.
Zu den Kunden zählen Elektroinstallateure wie beispielsweise Atel, Burkhalter, CKW und EKZ, Betriebe der öffentlichen Hand wie die Bundesbetriebe sowie Industrieunternehmen. Nicht beliefert werden Detailhandelsketten (Baumärkte) und Privatkunden, um keine eigenen Kunden zu konkurrenzieren. Eine besondere Dienstleistung der OFAG ist, dass auch Kleinstmengen bezogen werden können. Der Kunde schätzt es, dass z.B. eine Steckdose im Einzel- und nicht nur im 6er-Pack bestellt werden kann.
Der Anteil an Internetbestellungen liegt bei knapp über 50 %. Bis in zwei Jahren wird ein Anteil von ca. 75 % erwartet. Rückläufig sind Telefon- (28 %) und Faxbestellungen (22 %). Es sind vor allem die Kleinunternehmen, die die Internetbestellung nutzen. In Grossunternehmen bestellen Mitarbeitende häufiger direkt ab Baustelle per Mobiltelefon. Garantiert wird die Auslieferung bis 7 Uhr am Folgetag, sofern Onlinebestellungen bis 18 Uhr und Telefon- und Faxbestellungen bis 17 Uhr eingehen. Täglich sind es rund 3'000 Bestelleingänge, die im Durchschnitt die Kommissionierung von 4'000 Paketen mit 12'000 Artikel erfordern.
Ab 19 Uhr gehen 34 Touren in die ganze Schweiz. Die OFAG nimmt die Auslieferung mit über 40 eigenen Fahrern grösstenteils selbst vor. Das Schweizerische Arbeitsgesetz (Art. 10) schreibt vor, dass die nächtliche Arbeit nicht ohne Bewilligung ausgeführt werden darf. Für die betroffenen Touren wurden der Otto Fischer AG die amtlichen Bewilligungen erteilt. Welches Ausmass ein aus dem Arbeitsgesetz resultierendes Nachtarbeitsverbot mit sich bringt, wird in Kapitel 2 näher erläutert.
Unternehmensvision
Otto Fischer strebt an, sich als Marktführer im Bereich Dienstleistungen für Schweizer Elektroinstallateure zu positionieren. Die stetige Optimierung der Prozesse gehört zu den notwendigen Aufgaben, damit sich das Unternehmen laufend den Kundenanforderungen anpassen kann.
Stellenwert von Informatik und E-Business
Der Informatik wird ein hoher Stellenwert beigemessen. Dies zeigt sich in der starken Prozessorientierung über alle Bereiche hinweg. Die permanente Optimierung des Kundenservices und der Lieferlogistik mit Informations- und Kommunikationstechnologien gilt als Leitgedanke. Roger Altenburger, Vizedirektor der Otto Fischer AG, formuliert den Stellenwert von Informatik und E-Business wie folgt: „Ohne Informatik geht bei uns gar nichts und ohne E-Business fast nichts.“ Im Weiteren wird ein hoher Wert darauf gelegt, dass neben dem ERP-System keine Insellösungen geführt werden. „Ist die IT aus einem Guss,“ so Altenburger, „dann gewinnen wir Skalenvorteile.“
2. Der Auslöser des Projekts
Ausgangslage und Anstoss für das Projekt
Auslöser für das Projekt war der Geschäftsprozess beim Kunden. Der Kunde will um 7 Uhr mit der Arbeit beginnen. Um diese Zeit muss er die bestellten Artikel erhalten haben. Der Kunde weiss aber i.d.R. erst gegen 17 Uhr am Vortag, welche Artikel er braucht. Dies verursacht eine hohe Zahl an Auftragseingängen gegen Ende der Bestellfrist, wie aus Abb. 1 hervorgeht.
Die OFAG kommt dem Bedürfnis der Kunden nach, bis 18 Uhr bestellen zu können. Dies bedeutet eine hohe Anforderung an die Mitarbeitenden in der Auftragsabwicklung innert kürzester Zeit. Die Arbeitseffizienz der Lagermitarbeitenden wurde bereits vor der Einführung der im Folgenden beschriebenen Lösung als optimiert angesehen. Die Einstellung von weiteren Mitarbeitenden war keine Alternative, sondern hätte nur dazu geführt, „dass man sich im Lager auf den Füssen herumtrampelt“. Regelmässig mussten Überstunden geleistet werden, was sich vor allem auf die Arbeitszeiten der Fahrer auswirkte und vor dem Hintergrund des Nachtarbeitsverbots (Arbeitsgesetz) zunehmend Sorge bereitete. Das Unternehmen stand somit vor der Frage, wie es auf physisch begrenzter Fläche wachsen könne, ohne einen Umzug in grössere Lagerräumlichkeiten vornehmen zu müssen.
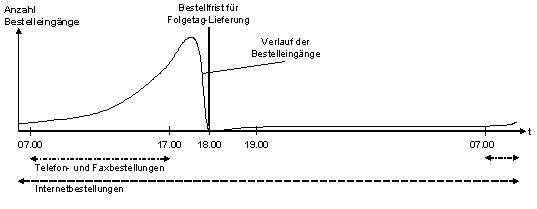
Abb. 1: Durchschnittlicher Verlauf der Bestelleingänge bei Otto Fischer
Ein Wechsel auf ein vollautomatisches Lager kam nicht in Frage, da eine Prüfung dieser Option eine starke Flexibilitätseinbusse aufgezeigt hatte. Dieses Risiko wollte die OFAG nicht in Kauf nehmen. In Zusammenarbeit mit der ETH Zürich wurde eine papierlose Kommissionierung untersucht [vgl. Hamprecht 2001]. Das Ergebnis der Studie erlaubte eine Abschätzung, inwieweit sich eine EDV-unterstützte Kommissionierung rentieren würde. Mit dem Ziel, die Spitzenzeiten abdecken zu können, wurde daraufhin ein Budgetrahmen für ein entsprechendes E-Business-Projekt definiert.
Vorstellung der Geschäftspartner
Otto Fischer arbeitet seit über zehn Jahren mit dem Informatikpartner Polynorm zusammen, mit dem sie in der Vergangenheit mehrere erfolgreiche Projekte umsetzten (z.B. die Einführung des E-Shops [vgl. Schubert 2000]). Aus Sicht der OFAG gab es keinen Anlass für eine Evaluation eines neuen Implementierungspartners. Für die mobile Lösung wurde die Firma Swiss1Mobile hinzugezogen, die die ERP-Lösung von Polynorm im mobilen Bereich ergänzt. Der Entscheid fiel zugunsten von Swiss1Mobile, obwohl dieser Softwareanbieter zwar die teuerste, aber eine individuell auf das Unternehmen angepasste Lösung offerierte.
Polynorm ist ein seit über 20 Jahren tätiges Schweizer Informatikunternehmen mit Spezialisten aus den verschiedensten Fachbereichen. Basis ihrer Geschäftstätigkeit ist die vollständig von ihnen entwickelte Standardsoftware i/2®, eine ERP-Lösung, die die Geschäftsprozesse der OFAG informatikseitig unterstützt.
Die Swiss1Mobile AG in Horgen konzentriert sich seit über vier Jahren auf mobile Lösungen. Bereitgestellt werden Hard- und Software, um mobilen Angestellten Zugriffsmöglichkeiten auf Daten und Funktionalität von Anwendungen im Unternehmen zu geben. Für die OFAG wurden über 100 mobile Mitarbeitende mit mobilen Geräten ausgerüstet.
3. Papierloser Warenfluss
Das langfristige Ziel der OFAG ist ein Bestellprozess zwischen Kunden und Anbieter, der von A bis Z papierlos abgewickelt wird. Der Kunde ruft die OFAG Website auf, bestellt online, bekommt die Ware und erhält die Rechnung elektronisch. Dies ist heute mit Ausnahme der Rechnung und dem Lieferschein in grossen Teilen umgesetzt. Mit einem ersten Pilotkunden wird derzeit die elektronische Rechnung getestet, und wenn die Kunden auch noch auf den physischen Lieferschein verzichten, wird in der gesamten Interaktion der Geschäftspartner kein Papier mehr erzeugt. Der aktuelle Grad der papierlosen Abwicklung wird in den folgenden vier Unterkapiteln illustriert.
Geschäftssicht und Ziele
In der Vergangenheit holte der Lagermitarbeitende einen Rüstschein bei der Lagerdisposition ab, nahm sich einen geeigneten Kommissionierwagen und entnahm einen Artikel nach dem anderen aus den Lagergestellen. Ein erfahrener Mitarbeitender konnte zwei bis drei Rüstscheine gleichzeitig abarbeiten. Dieses Verfahren führte jedoch dazu, dass zu Spitzenzeiten Warteschlangen und Behinderungen auf den Kommissionierstrassen entstanden.
Heute kann ein Mitarbeitender bereits nach kurzer Einarbeitungszeit bis zu 18 Aufträge gleichzeitig bearbeiten. Möglich ist dies mit einem mobilen Datenerfassungsgerät (MDE-Gerät), das den Mitarbeitenden steuert und ihn somit Schritt für Schritt auf einer wegoptimierten Route durch das Lager führt.
Die mobile Datenerfassung ermöglicht es, Daten abseits vom PC-Arbeitsplatz zu erfassen. Durch den Einsatz von Barcodescanner sind Daten sofort elektronisch verfügbar und können, nach Einspielung in das System, von diesem bearbeitet und ausgewertet werden. Auf diese Weise werden Medienbrüche vermieden und die Datenerfassung wird beschleunigt. Mit diesem Konzept unterstützt OFAG heute den gesamten Warenfluss.
Wie in Kapitel 2 aufgezeigt, war der Kommissionierprozess bei Otto Fischer der Engpass im Warenfluss. In den vergangenen Jahren wurden die Bestellmöglichkeiten für den Kunden optimiert, was dazu führte, dass heute von den über 50 % Internetbestellungen rund 90 % automatisch disponiert werden können. Lediglich 10 % der Bestellungen erfordern manuelle Korrekturen und werden von der Auftragsannahme kontrolliert und angepasst. Der optimierte Auftragseingang erfordert ein effizientes Lagerwesen, mit dem Ziel, dass alle Aufträge innert Frist zum Versand (Spedition) bereitstehen. Ohne E-Business wäre dies bei der OFAG nicht denkbar. Abb. 2 zeigt eine Übersicht über den Bestell- und Warenfluss.
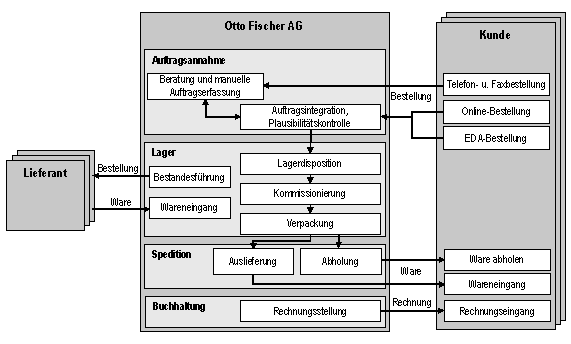
Abb. 2: Übersicht über den Bestell- und Warenfluss
Mit der Lösung wurde auch der Wareneingang optimiert, der heute in drei Stufen erfolgt. Nach der Warenanlieferung wird eine interne Durchgangsauszeichnung vorgenommen. Da kein Papier mehr verwendet wird, bekommt die Ware ein Etikett mit einem Wareneingangscode aufgeklebt. Ab diesem Zeitpunkt kann der Artikel mit den MDE-Geräten gescannt und somit jederzeit identifiziert werden. Der Artikel wird anschliessend am entsprechenden Lagerplatz gelagert.
Neben den Lagermitarbeitenden wurden auch die Fahrer mit MDE-Geräten ausgerüstet, denn der papierlose Warenfluss ist konsequent bis zur Warenübergabe beim Kunden umgesetzt. Beim Verladen der Sendungen in die eigene Transportflotte wird jedes Gebinde gescannt, wodurch der Speditionsdisponent jederzeit detaillierte Informationen zum Arbeitsfortschritt der einzelnen Liefertouren erhält. Der Fahrer bestätigt das Abladen beim Kunden durch Scannen der einzelnen Gebinde. Diese Informationen sind nach der Beendigung der Tour im ERP-System verfügbar.
Prozesssicht
Abb. 3 zeigt den Prozess der Kommissionierung. Im System ist zu jedem Lagermitarbeitenden ein Profil hinterlegt, das Auskunft über Arbeitskenntnisse und Präferenzen gibt (z.B. ob die Person spezielle Gebinde bearbeiten kann). Die Kommissioniertätigkeit beginnt mit der Anmeldung am MDE-Gerät. Danach wird dem Mitarbeitenden, vom System ein Kommissionierauftrag zugeteilt.
Die eingehenden Kundenaufträge [Auftrag] werden alle im ERP-System erfasst, unabhängig, ob der Kunde telefonisch, elektronisch oder vor Ort bestellt. Ist ein Lagermitarbeitender angemeldet und verfügbar, prüft das System zuerst, ob ein Expressauftrag vorliegt. Dieser wird mit Priorität behandelt und dem Mitarbeitenden als Einzelauftrag zugeteilt. Sofern keine Expressaufträge vorliegen, stellt das System einen Sammelauftrag zusammen, der aus bis zu 18 Aufträgen mit ähnlichen Inhalten besteht. Die Zusammenstellung berücksichtigt im Weiteren, dass Gebinde des gleichen Typs verwendet werden, und berechnet den optimalen Kommissionierweg durch die Lagerhallen. Dieser Schritt zur Erzeugung eines Kommissionierauftrags (1) erfolgt vollautomatisch. Für die Lagerdisponentin bleibt der Mitarbeitendenansturm zur Fassung von Rüstscheinen erspart, da sie heute per Knopfdruck dem verfügbaren Mitarbeitenden einen seinem Profil entsprechenden Auftrag zuweist.
Die anschliessende Vorbereitung zur Kommissionierung (2) bedingt zuerst eine Auftragsannahme durch den Mitarbeitenden. Möchte die Person z.B. eine Pause einlegen, kann sie den Auftrag zurückweisen. Die Gruppierung, die vorgeschlagen wurde, wird dann wieder aufgelöst, da bereits nach wenigen Minuten ein optimaler Sammelauftrag ganz anders aussehen kann. Bestätigt die Person den Auftrag, werden ihr auf dem MDE-Gerät Kommissionierwagen und Gebindetyp (OFAG führt gegen 30 Gebindearten) sowie Anzahl der notwendigen Gebinde angezeigt. Die OFAG hat im Rahmen der Einführung mobiler Erfassungsgeräte neue Kommissionierwagen konzipiert, die ein einfaches Befördern der Gebinde durch das Lager erlauben. Zudem ist an jedem vorgesehenen Gebindeplatz auf den Kommissionierwagen ein Barcode angebracht. Mit dem Scannen des Barcodes auf dem einzelnen Gebinde und dem Scannen des zugewiesenen Gebindeplatzes sind die Gebinde je Auftrag eindeutig identifiziert.
Jetzt beginnt der eigentliche Kommissionierprozess (3) [Logistik]. Das System zeigt die erste Rüstposition an. Angegeben werden das aufzusuchende Lagergestell, die Artikelnummer und die entsprechende Menge je Gebinde, in die der Artikel zu kommissionieren ist. Sofern die bestellte Menge den gehaltenen Lagerbestand überschreitet, vermerkt der Mitarbeitende die fehlende Menge, worauf automatisch eine Nachbestellung veranlasst wird. Danach bestätigt der Mitarbeitende die entnommenen Mengen und sogleich wird ihm der nächste Rüstauftrag zugewiesen. Dies wiederholt sich solange, bis alle Gebinde mit den entsprechenden Artikeln gefüllt sind.
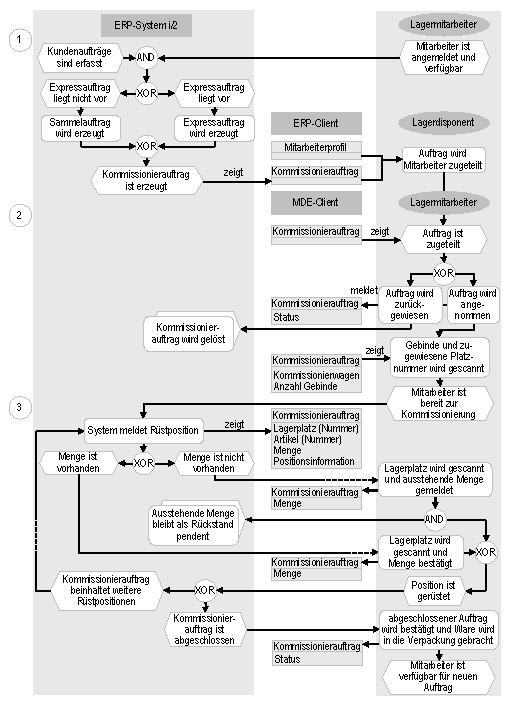
Abb. 3: Papierloser Warenfluss in der Kommissionierung
In Ausnahmefällen (z.B. bei wenig erfahrenen Mitarbeitenden) verlangt das System, dass jeder Artikel gescannt werden muss. Dies reduziert zusätzlich die Gefahr einer Verwechslung.
Ist der Kommissionierauftrag abgeschlossen, bringt der Mitarbeitende die Gebinde in die Verpackungsabteilung, die ebenfalls vom ERP-System barcodegesteuert unterstützt wird. Der Lieferschein wird beim letzten Teilrüstauftrag einer Bestellung ermittelt und ausgedruckt.
In der Regel werden die Bestellungen durch die eigenen Fahrer ausgeliefert. Nur einzelne Pakete werden per Post versandt. Beim Verladen der Sendungen in die Fahrzeuge wird jedes Gebinde gescannt, wodurch der Speditionsdisponent jederzeit detaillierte Informationen zum Arbeitsfortschritt der einzelnen Liefertouren hat. Der Fahrer bestätigt die Anlieferung beim Kunden wiederum durch Scannen der einzelnen Gebinde. Diese Informationen sowie vom Fahrer zusätzlich erfasste Daten (wie Angaben zur Tankfüllung, Kilometerstand oder individuelle Anmerkungen) sind nach der Beendigung der Tour im ERP-System verfügbar.
Des Weiteren ist der gesamte Wareneingang, die Reservelagerverwaltung und die Nachschuborganisation papierlos mit der gleichen Informatiklösung abgedeckt. Durch den Aufbau eines Funknetzes (WLAN) im Lager können zudem mobile Desktops für aufwändigere Arbeiten wie Lagerinventur direkt am Lagergestell eingesetzt werden.
Anwendungssicht
Nachdem die Prozesssicht die Interaktion zwischen MDE-Gerät und ERP-System veranschaulicht, wird im Folgenden der Datenaustausch zwischen den einzelnen Systemen näher vorgestellt (vgl. Abb. 4).
Kunden bestellen online über den E-Shop oder nutzen die XML-Schnittstelle für den elektronischen Datenaustausch (EDA). Diese, wie auch die in der Auftragsannahme erfassten Bestellungen, sind anschliessend im ERP-System verfügbar, wo die Generierung der Sammelaufträge zur Kommissionierung vorgenommen wird. Die zugeteilten Lagermitarbeitenden arbeiten direkt auf dem ERP-System. Auf dem MDE-Gerät läuft eine Emulationssoftware, die über das WLAN den direkten Zugriff auf das ERP-System erlaubt. Auf diese Weise kann auf die benötigten Informationen zugegriffen werden, ohne dass auf dem Gerät selbst Daten gespeichert sind. Der MDE-Client (1) der Lagermitarbeitenden ist eine reduzierte, mobile Alternative zum ERP-Client.
Die MDE-Lösungen (2) der Fahrer haben einen erweiterten Funktionsumfang. Für sie ist es wichtig, dass die Tourendaten für die Auslieferung auch ausserhalb der WLAN-Zone verfügbar sind. Deshalb verfügen die Geräte der Fahrer neben einer Emulationslösung zusätzlich über eine Datenaustauschfunktion, damit strukturierte Inhalte der Tagestour offline einsehbar sind. Sobald ein Fuhrauftrag definiert ist, werden die Daten in komprimierter Form auf den Swiss1Server gespielt (einfacher File Transfer), von wo aus sie über das WLAN geladen werden können.
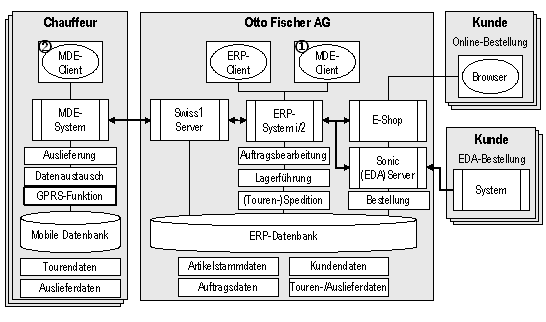
Abb. 4: Anwendungsübersicht und Integrationsschema
Von den 40 Lösungen der Fahrer ist die Hälfte mit einer GPRS-Funktion ausgestattet. Damit ist die ortsunabhängige Datenübermittlung möglich. Diesen Gerätetyp verwenden insbesondere die Fahrer, die die Ware ausserhalb der WLAN-Zone z.B. an einem Umschlagplatz entgegennehmen. Nach Abschluss einer Tour baut der Fahrer erneut eine Verbindung mit dem Swiss1Server auf und schickt das Datenpaket mit den Ausfuhrdetails wie z.B. den Zeiten, wann er wo welche Pakete abgeladen hat, zurück.
Technische Sicht
In Abb. 5 sind die für das MDE-Projekt relevanten Netzwerke und Systeme aufgeführt. Die Wireless LAN-Zone ist mit 22 Access Points bestückt und erstreckt sich über das Lager und die Ladezone. In diesen Bereichen können alle Lagermitarbeitenden und Fahrer mit MDE-Geräten direkt auf das ERP-System via WLAN zugreifen. Details zu den zentralen Systemen sind in Tab. 1 aufgeführt.
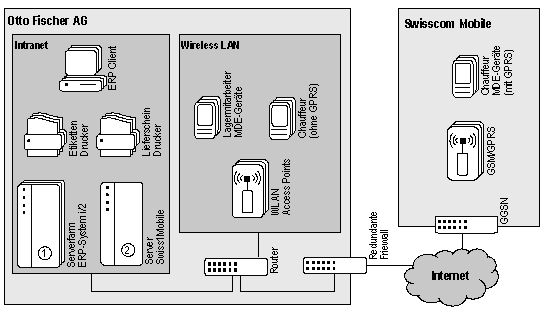
Abb. 5: Netzwerk und Systeme
Ausserhalb des WLAN kommunizieren die Fahrer mit GPRS-Geräten über das GSM-Netzwerk von Swisscom Mobile und dem Internet mit dem Swiss1Mobile-Server. Swisscom Mobile bietet den Zugriff aus dem GSM-Netz in das Internet über einen Gateway GPRS Support Node (GGSN) an. Der GGSN wandelt die GPRS-Datenpakete in TCP/IP Pakete um.
Tab. 1: Spezifikationen und Merkmale
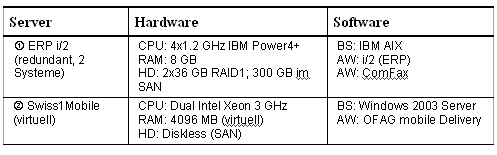
CPU: Prozessor, RAM: Arbeitsspeicher, HD: Festplattenspeicher
BS: Betriebssystem, AW: Anwendungssoftware, MW: Middleware, DB: Datenbanksoftware
4. Projektabwicklung und Betrieb
Projektmanagement und Changemanagement
Das Projekt konnte in einem straffen Zeitplan umgesetzt werden. Dies war insofern notwendig, da der Termin für den Go-life auf den Juli fixiert war, dem einzigen Monat, in dem eine Prozessanpassung in diesem Ausmass denkbar war. Bei einer Projektverzögerung wäre die Einführung um ein Jahr verschoben worden. Die Grundlagen für das Projekt wurden im Jahr 2004 erarbeitet. Es gab Vorbesprechungen mit den Partnern, Kostenschätzungen und Investitionsrechnungen. Darauf wurde der Projektstart auf Januar 2005 mit dem Ziel festgelegt, ab Juli die neue Lösung zu benutzen.
[Realisierung] Die Konzeptphase dauerte drei Monate und wird heute als äusserst wertvoll betrachtet. Es wurden Mitarbeitende involviert, die die Prozesse selbst kennen und ausführen. Mehrmals kam es bei der Aufnahme der einzelnen Prozessschritte dazu, dass individuelle Arbeitsgewohnheiten von Mitarbeitenden deutlich wurden, die zwar den Prozess verlängern, sich aber für ein effizientes Arbeiten als notwendig erwiesen. Bis Ende März wurde ein Pflichtenheft erstellt, anhand dessen Polynorm die Lösung programmierte. Ab April fanden Schulungen statt. Zuerst wurde anhand von Screenshots geschult. Ab Mai waren die ersten Programme für Liveschulungen verfügbar. Es gab eine aufwändige, aber sehr erfolgreiche Testphase, die an zwei Samstagen mit jeweils rund 80 Mitarbeitenden stattfand und in der die Prozessabläufe durchgespielt wurden.
Entstehung und Roll-out der Software-Lösung
Obwohl die Lösung speziell auf die Bedürfnisse des Standortes angepasst ist und dadurch eine gewisse Einmaligkeit aufweist, wurde darauf geachtet, dass die Release-Fähigkeit gewährleistet bleibt. Die Programmierung der i/2-Komponente für die ERP-Erweiterung konnte anhand des erarbeiteten Pflichtenhefts und den dabei gewonnen Prozesskenntnissen weitgehend problemlos umgesetzt werden. Herausfordernd war die EDV-technische Abdeckung von Spezialwünschen zu Prozessabläufen.
Laufender Unterhalt
Lange Antwortzeiten auf den MDE-Geräten waren ein Grund für anfängliche Sorgen mit dem Funknetz. Swiss1Mobile nahm darauf mit einem neuen Produktanbieter Kontakt auf und das Netzwerk wurde in der Folge neu erstellt. Mit dem Funknetz ist man heute zufrieden, jedoch mussten alle Geräte der Fahrer wegen Hardware-Problemen ausgetauscht werden. Im Lager hat sich bewährt, dass auf die Geräte lediglich Position für Position geladen wird und nie ein ganzer Auftrag. Dies vermeidet das Risiko von Datenverlust und erlaubt einem Mitarbeitenden bei Gerätausfall ein umgehendes Anmelden und Weiterarbeiten auf einem neuen Gerät.
5. Erfahrungen
Nutzerakzeptanz
Die Umstellung auf den papierlosen Betrieb hatte zur Folge, dass die handschriftliche Informationserfassung abgelöst wurde. Eine unter den Mitarbeitenden über die Jahre eingespielte Notizsprache wie z.B. ein Verweis auf doppelte Kontrolle bei einzelnen Kundenaufträgen finden in einem Sammelrüstscheinkonstrukt, wie es heute besteht, keine Berücksichtigung mehr und bedeutet den Wegfall von Gewohnheiten. Die anfangs befürchteten Reklamationen bezüglich zu kleiner Bildschirmen oder zu schwacher Kapazität traten nicht ein. Im Gegenteil, es wird von einer Musterlösung gesprochen, die man gerne weiterempfiehlt.
Zielerreichung und bewirkte Veränderungen
OFAG strebte mit der Einführung der Geräte zur mobilen Datenerfassung eine Reduktion der Durchlaufzeit, Kapazitätserweiterung und -flexibilisierung, Reduktion der Prozesskosten, Reduktion der Fehlerquote und Erhöhung der Prozesssicherheit sowie Vereinfachung der Prozesse an. Diese Ziele wurden ausnahmslos erfüllt. Bemerkenswert ist auch die mit dem Einsatz von Informatik gewonnene Effizienzsteigerung der Arbeitsleistung eines jeden einzelnen Mitarbeitenden, und dies aus einem Zustand heraus, der bereits als optimiert bezeichnet wurde.
Ein Mitarbeitender rüstete früher pro Stunde 58 Positionen. Die Kapazität konnte um 23 % auf durchschnittlich 72 Positionen erweitert werden. Gleichzeitig konnte der Mitarbeitendenbestand im Lager trotz steigender Positionswerte leicht reduziert werden. Die Fahrer, für die regelmässig 1.5 Stunde Abfahrtsverzögerung die Regel war, können heute pünktlich um 19 Uhr ihre Touren starten. Vereinfacht wurden die Prozesse im Lager vor allem durch die optimierten Kommissionierwege, so dass kein Stau auf den Lagerstrassen mehr entsteht. Die Fehlerquote von 0.5 % Positionsfehler im Jahr 2003/04 (was schon damals als sehr gut bezeichnet wurde) ist seit Februar 2006 auf 0.18 % zurückgegangen. Gesetztes Ziel war 0.2 % und nach heutiger Einschätzung wird man langfristig sogar bei 0.15 % liegen. Die Fehlerreduktion bringt hohe Einsparungen dank dem Wegfall von unproduktiven Prozessen, d.h. Mehrfachkommissionierung und Verzögerungen in Spedition und Auslieferung. Selten wird bei der Kommissionierung Ware in die falschen Gebinde gelegt. Bei der Auslieferung treten heute keine Fehler mehr auf, weil das System dem Fahrer die Weiterfahrt nicht freigibt, bis die richtigen Pakete gescannt sind.
Investitionen, Rentabilität und Kennzahlen
Budgetiert wurden 1.25 Mio. CHF. Durch eine effiziente Projektarbeit konnte der Budgetrahmen eingehalten werden. Finanzielle Aspekte waren bei der Suche nach einer geeigneten Lösung von sekundärer Bedeutung – das hat man den Partnern von Anfang an kommuniziert. Jedoch bestand man darauf, dass das Budget eingehalten wurde. Bereits heute steht fest, dass der im Vorfeld auf unter drei Jahre berechnete Return on Investment (ROI) problemlos in kürzerer Frist erreicht werden wird.
Die mobile Softwarelösung für die Fahrer macht rund 10 % der gesamten Projektkosten aus. Für ein MDE-Gerät wurden 3'000 CHF, inklusive GPRS-Funktion 5'000 CHF bezahlt. Im Rahmen dieses Projekts wurden zusätzlich sechs Etikettendrucker (je 5'000 CHF) angeschafft. Die Kosten für das Funknetz (WLAN-Zone) lagen bei 40'000 CHF.
Die intern angefallenen Projektkosten sind nicht zu unterschätzen, können aber nur schwer beziffert werden. Besonders der Projektleiter war während der Projektzeit stark zusätzlich belastet. Darüber hinaus waren permanent zwei bis drei interne Mitarbeitende für das Projekt engagiert.
6. Erfolgsfaktoren
Spezialitäten der Lösung
Eine Spezialität der mobilen Lösung ist die Anbindung ans ERP-System. Dadurch sind die Mitarbeitenden während ihrer Tätigkeiten optimal mit elektronischen Informationen bedient. Unterschieden werden Geräte der Fahrer mit lokaler Speichermöglichkeit und so genannte reine Emulationslösungen für Lagermitarbeitende. Für eine hohe Benutzerakzeptanz sorgt der zur Verfügung stehende Funktionsumfang. Der Mehrwert für den Mitarbeitenden liegt dabei in der Reduktion der für ihn notwendigen Funktionen, was ein effizientes und sicheres Arbeiten erlaubt.
Reflexion der „Prozessexzellenz“
Die Firma Otto Fischer hat die Vision eines papierlosen Prozesses für ihre Auftragsabwicklung verwirklicht. Innert kürzester Zeit konnte der Kommissionierprozess in einer Interaktion zwischen Mensch und Maschine derart effizient gestaltet werden, wie es gegenwärtig nach Meinung der Beteiligten mit keinem vollautomatischen Lagersystem günstiger zu lösen wäre. Der Kunde kann dadurch bedürfnisgerecht beliefert werden in einem Ausmass, das der OFAG das Vertrauen gibt, der Konkurrenz heute einen Schritt voraus zu sein.
Lessons Learned
Der blosse Einsatz von MDE-Geräten alleine garantiert noch keine Effizienzsteigerungen. Der Erfolg zeigt sich dann, wenn die Mitarbeiteraktivitäten mit den vom System unterstützten Prozessen harmonieren. Ein MDE-Projekt ist demnach immer ein Individualprojekt. Otto Fischer und Polynorm starteten das Projekt mit einer intensiven Konzeptionsphase. Vor dem Hintergrund der Erfahrungen würde Herr Altenburger heute bei der Implementierung in zwei Projektphasen vorgehen. Die gleichzeitige Einführung der mobilen Lösung in der Spedition, in der Kommissionierung und im Wareneingang erforderte eine (zu) hohe Betreuungsintensität. Darüber hinaus darf eine angemessene Kommunikation unter Mitarbeitenden und Kunden rund um das technische Projekt nicht vernachlässigt werden.