EDEKA Minden-Hannover: Electronic Invoice Transfer
EDEKA Minden-Hannover Holding GmbH (hereafter referred to as "EDEKA") is the market leader in its trading area and the most important EDEKA regional company, driving innovation within the EDEKA Group. Numerous local suppliers deliver retail products to the company. Until 2006, suppliers sent paper invoices to EDEKA by post. The internal process at EDEKA was complicated, multi-level, and not transparent for suppliers. A new solution has been rolled out by means of which electronic invoices are transferred automatically in a process that is transparent for EDEKA's suppliers. The process is more cost-effective for suppliers and for EDEKA and the process lead times have been reduced.
table des matières
1. The Company2. What Triggered the Project
3. Electronic Invoice Transfer
Business Perspective , EBPP, Process Perspective , Data Exchange, Invoice Receipt , Application Perspective , Technical Perspective
4. Project Flow and Operation
Project Management, Roll-out
5. Experiences
Investments
6. Success Factors
E-Collaboration
1. The Company
Background, Industry, Product, and Target Group
With Group sales of EUR 5 billion, 24,300 employees, approximately 1,500 retail locations, and a total sales area of 1.3 million square meters, EDEKA Minden-Hannover is the largest of the seven EDEKA regional companies in Germany. Its core business is food retail.
The EDEKA supermarkets, which are geared towards quality and service, can be classed as complete service providers in particular thanks to their expertise in the food industry.
EDEKA's current advertising slogan, "Wir lieben Lebensmittel" (we love food) is currently being communicated in newspaper, magazine, TV, and radio adverts.
EDEKA's various sales formats allow it to tailor its retail offering to local requirements. Two thirds of EDEKA Minden-Hannover's supermarkets are managed by independent traders, who are organized in a cooperative within EDEKA Minden eG, the parent company of the group.
Transferring EDEKA supermarkets to independent traders and entrepreneurs also plays a key role in planning. This is how EDEKA fulfills its corporate mission, which is defined in the charter of the cooperative as being to create economically secure, fully viable operations run by independent business people in the medium-sized food retailer industry and related professional groups and to promote and sustain these.
EDEKA creates competitive advantages for itself by means of entrepreneur-led retail: Entrepreneurial engagement has a strong presence on location, which is rewarded by customers and employees alike. Products typical to the local region are also sold.
Inventory management and logistics are key success factors in the highly competitive food retail industry. With eight warehouses, four load transfer points, and two drinks warehouses, EDEKA Minden-Hannover's logistics operations are distributed to create optimal conditions for meeting retail requirements.
With 25 superstores, MIOS C+C specialist wholesale traders caters to the needs of bulk consumers such as hotels, restaurants, and businesses.
EDEKA Minden-Hannover has its own production plants for the key product segments of freshly baked goods and meat and sausage products. The trading area extends from the Polish to the Dutch border and is concentrated in Saxony-Anhalt, Bremen, Berlin, Brandenburg, and Lower Saxony.
Corporate Vision
"What do we at EDEKA Minden-Hannover stand for, what values do we aim to live by, how do we want to set ourselves apart from the competition, and what goals do we set ourselves? This answers to these questions can be found in our VISION and our MISSION, which together make up our corporate philosophy.
We don't just sell food, therefore, we love food! That is our VISION. It influences our thoughts and actions. It is our message to our customers and business partners. And because we love food, no one has more expertise in the food industry than EDEKA.
We must back up this statement every day in our supermarkets through our range of products, shop layout, presentation of products, and quality and freshness, but also in particular through the expert advice and service quality provided by our employees." [Translated extract from the Executive Board Report of EDEKA Minden-Hannover, May 2, 2006]
Importance of IT and E-Business
EDEKA operates in a market in which customer needs are constantly changing, as are the general legal conditions within an open European Union. To be able to live up to the standards set out in our vision with a consistently high level of intensity and quality, we require a flexible, high-performance IT infrastructure that is capable of fulfilling the requirements of a process-oriented organization quickly and efficiently.
EDEKA Minden-Hannover plays a leading role in exchanging logistics messages by Electronic Data Interchange (EDI) and applying the European Article Number Commercial (EANCOM) standard. As a result, a working group of GS1 Germany GmbH used the digital acceptance document developed by EDEKA Minden-Hannover as the basis for defining a standard for the food industry.
By using electronic workflows and collaborating with a service provider in the area of electronic invoice transfer, EDEKA Minden-Hannover enables its business partners, who are mostly SMEs, to use and benefit from EDI.
2. What Triggered the Project
Initial Situation and Trigger for the Project
Most suppliers have to invoice EDEKA several times a month for the deliveries they make. At the same time, service providers and companies that have sold benefits in kind to EDEKA must also send invoices to EDEKA. Due to its large number of regional suppliers, EDEKA receives over 440,000 invoices a year. Each invoice is subject to a multi-level internal verification and release process. Various organizational units, some of which operate at different locations, are involved in this process. Information is mainly exchanged in paper format. Paper documents are exchanged manually by the organizational units involved.
The project presented here was triggered by the goal of replacing the manual paper-based invoicing process with a semi-automated electronic solution. The main aims of the solution were to improve the processes within EDEKA and to simplify the process by which suppliers invoice EDEKA, and in doing so to render all processes transparent.
Our Business Partners
EDEKA's IT partner in the project presented here was FIRST BUSINESSPOST GmbH (1stbp). 1stbp is a young company that was founded in 1999 and won the "Bayern Online Award for E-Business" in 2004. 1stbp offers a solution for paperless invoicing. Two characteristics set this solution apart: The sender of an invoice is able to use EDI by means of simple software, and the paper problem at the recipient is resolved permanently, cost efficiently, and effectively. As an EDI service provider, 1stbp acts as an intermediary between senders and recipients.
3. Electronic Invoice Transfer
In the following sections, the solution is considered from a business, process, application, and technical perspective. The focus is on the actual core invoicing process, processing the invoice at EDEKA, and integrating suppliers and 1stbp as the service provider in this process.
Business Perspective and Goals
EDEKA mainly receives two different types of invoice. On the one hand, it receives invoices from suppliers who deliver goods for EDEKA's wholesale and retail operations (goods invoices). The supplier sends an invoice after it has made a delivery. The second type of invoice comes from companies who provide services, benefits in kind, or goods (investments) for EDEKA's own use and who must, therefore, send EDEKA an invoice with an attachment (bills of charges). These invoices are labeled internally by EDEKA as bills of charges or internal requirements invoices and are not related directly to value creation. When the invoice is created, the services or benefits in kind are described, for example, the number of hours and the material required to render a service.
The following sections describe a simple invoicing process from the supplier's perspective. The process for invoices with attachments is identical except that the attachments are subject to an additional check by the organizational unit responsible at EDEKA.
Fig. 1 shows the process by which a supplier invoices EDEKA. This process can be executed in one of three different ways. Within the scope of offline invoicing, the invoices can be sent to EDEKA by post. These invoices are scanned and converted to electronic documents using an OCR program. Only the invoice header data is read. These documents must then be revised manually. A multi-level verification process is then carried out and the invoices are released and then paid.
The second option for suppliers is to use central regulation at EDEKA's headquarters. A contract, for which a charge is payable, must be concluded to this end between the supplier and EDEKA's headquarters. The data is transferred electronically by means of EDIFACT, but without a qualified signature or attachments. This means that a paper-based collective invoice must also be sent. An in-house data record is also sent simultaneously to EDEKA Minden and transferred to the invoice verification program.
The third option is to use the new, fully electronic solution provided by 1stbp[EBPP]. A special printer driver must be installed at the supplier for printing the invoices. The print data stream is diverted to a file instead of being output physically on paper. This file is then transferred to the e-mail program by means of a MAPI. The resulting e-mail is sent to the processing center at 1stbp, where the relevant information is extracted from the print data streams, verified, and converted to the target format using a specially developed ruleset in a Java-based Internet gateway. Besides submitting print data streams by e-mail, additional transport protocols and formats are available to the supplier. The variant described here is merely one of the possible options.
In the Internet gateway the data is entered, checked for completeness, prepared for the recipient, and made available for download. An automatic process for downloading the electronic invoices is in place at EDEKA. These invoices are then immediately sent for verification and then normally released for payment. The supplier can view the status of the invoice at each step. He can check the status of the invoice online at 1stbp to see whether it has already been processed or forwarded to EDEKA, for example.
Fig. 1: Business Scenario: Invoice Processing at EDEKA
Process Perspective
Fig. 2 shows the electronic invoice transfer process [Data Exchange]. The supplier prints the invoice he wants to send to EDEKA from his accounting application using a "virtual printer" in a single or mass print run. The printer installed generates a print data stream (postscript) of the invoice to be printed in the form of a file and then encrypts and signs this file. The data is then sent to 1stbp by e-mail using the standard e-mail program or stored as a file in a configurable directory, the contents of which are then sent to 1stbp. The data is received by a processing system at 1stbp[invoice receipt]. This processing system uses a specially developed ruleset to extract the contents of the print data stream and initially stores the resulting data in an internal data format.
After the transfer, the data is checked for syntactical correctness. This includes a check that the invoice is arithmetically correct, the service data is correct, no duplicate invoice numbers have been assigned, all fields defined by EDEKA as mandatory (such as the cost center) have been maintained, and so on. If errors occur during the check, an error message is issued and the supplier informed of this by e-mail. The supplier must then revise and correct the invoice and send it again. If the data is correct, it is converted to the format specified by EDEKA (EDI). An image file of the original invoice is also generated. The files are then encrypted and signed using an electronic signature of Deutsche Telekom/Telsec, an approved certification provider in Germany (hereafter referred to as "Trust Center") in accordance with Section 14 of the German Turnover Tax Act (UStG). Only once this signature has been provided does the (electronic) document entitle the recipient to input tax.
EDEKA downloads the encrypted invoices from 1stbp by means of HTTP at configurable time intervals. The data is decrypted by the 1stbp download manager and the integrity of the invoice is verified. The authenticity of the certificate used for the signature is also verified. To this end, online certificate status protocol (OCSP) requests are used to check that the certificate exists at the issuing Trust Center and is not blocked. The certificates of the Trust Center are then checked recursively against the root certificate of the German Federal Network Agency (Bundesnetzagentur) and the result recorded in a check log. All the information that must be retained is then transferred to the archiving system. This includes the original invoice (as an image file), the certificates, and the check log.
The invoice data entered in EDI format is then transferred to the invoice verification and workflow system. The workflow system informs the organizational unit responsible for verifying the invoice that the invoice data is available and this organizational unit then verifies the contents of the invoice. If errors occur here, an error message is issued and the supplier is informed of this by e-mail. The supplier must then revise and correct the invoice and send it again with a new invoice number. Invoices whose contents are correct are posted and paid.
Fig. 2: Process Perspective: Electronic Invoice Processing at EDEKA Minden-Hannover
Application Perspective
Now that the individual steps required for electronic invoicing have been described from a process perspective, this section goes on to describe data exchange within the scope of a successful electronic invoicing process between the individual software systems of the suppliers, 1stbp, and EDEKA (see Fig. 3). The supplier prints his invoice using the "virtual printer", which 1stbp provides free of charge, and an encrypted print data stream is then created containing the invoice data.
Fig. 3: Application Perspective and Integration Scheme, EDEKA Minden-Hannover
This data stream is sent to the processing system at 1stbp, which extracts, verifies, and converts the data to the data format relevant for EDEKA.
The converted invoice is then encrypted, provided with a qualified signature, and made available for EDEKA to download. 1stbp stores status information, which the supplier can then access. This includes information about whether and when the invoice data arrived at EDEKA. The download manager at EDEKA accesses the processing system at 1stbp periodically to retrieve the invoice data and certificates. The data is decrypted and the certificates checked. The invoice data is forwarded to the invoice verification system and the original invoice, certificate, and check log are sent to the archiving system. When the workflow system is activated, the organizational unit responsible is prompted to verify the invoice.
Technical Perspective
Suppliers, who operate at different locations, send the invoice data to 1stbp as a print data stream or structured data record using various protocols. 1stbp then enters and converts this data at its processing center and makes it available for EDEKA to download.
Fig. 4: Technical Perspective, EDEKA Minden-Hannover
Communication between the individual systems (see Fig. 4) of the suppliers, 1stbp, and EDEKA mainly takes place over the Internet, either by e-mail (SMTP), HTTP, AS2 (exception: x.400) between the suppliers and 1stbp or by HTTP between EDEKA and 1stbp. All of the data that is exchanged over the Internet is encrypted and signed.
No special hardware is required to integrate the 1stbp electronic invoice transfer solution. 1stbp provides clients for a wide range of operating system configurations that can be integrated easily in the existing systems of the suppliers. EDEKA procured new hardware on which to run the download manager provided by 1stbp.
4. Project Flow and Operation
Investment Decision
The internal costs incurred at EDEKA for traditional processing of a paper-based invoice amount to EUR 2 per invoice. This is a very low benchmark, since it includes the costs for scanning, postprocessing, multi-level verification, and release of the invoice as well as telephone support in the event of queries from suppliers and any necessary postage costs. The costs for procuring hardware and programming the interfaces were estimated at approximately EUR 40,000. On the other hand, potential savings amounted to EUR 200,000 – 400,000 a year, assuming a cost reduction of one Euro per invoice. The investment decision was made within the scope of an Executive Board meeting and the switch to electronic invoicing defined as a corporate goal.
Project and Change Management
The project was initiated by Group Quality Management. The project team comprised members from all areas of EDEKA affected by electronic invoice processing. This included employees involved in invoice verification, logistics, IT, accounting, and auditing. This made it possible to take account of the requirements of the specialist departments from an early stage and integrate them in the new solution.
A key aspect of the rollout of the new electronic invoicing process was the reorganization of the internal processes for verifying and releasing invoices. Before electronic invoicing was introduced, the invoices had to be scanned and verified, which now happens automatically at 1stbp. The periodic verification and release process was complex, sometimes involving more than eight organizational units and several locations. This could sometimes take a long time, for example, if the supplier sent incorrect invoices. The processes for verifying and releasing the invoices were completely reorganized. The only check still carried out is that by the organizational unit responsible for the invoice to ensure that its contents are correct. Once the invoice has been verified and released, it is posted and passed for payment automatically. The individual specialist departments were actively informed about the new system and employees received training in how to use the new processes and software.
Development and Rollout of the Software Solution
Several interfaces had to be implemented at EDEKA for electronic invoice processing to make the data provided by the download manager available to the internal EDEKA systems such as the archiving, workflow, and invoice verification systems. The finished solution was tested with selected suppliers for two months within the scope of a pilot phase, then commissioned within the scope of a further validation phase two months before the full rollout.
Continuous Maintenance
A key advantage of the solution is that EDEKA did not have to install any additional external software apart from the download manager. The interfaces programmed by EDEKA are maintained separately from changes to the download manager, since the download manager makes the data available in a file-based format. Since employees from a wide variety of organizational units at EDEKA were involved in the design and project rollout phases, no significant new requirements arose during operation. The fact that an image file that looks exactly the same as the paper invoice used previously is transferred as part of the workflow in addition to the data record resulted in a very high level of user acceptance.
5. Experiences
User Acceptance
The experiences gained over the first six months were wholly positive. The transparency of the invoicing process from the suppliers' perspective and the significantly faster release and payment of invoices are seen by all participants as positive developments.
The changes regarding responsibility for verifying and releasing the invoices at EDEKA were also received well. Invoices are now verified and released immediately by the organizational units responsible. It is now no longer necessary to maintain item data manually for each cost center. This data is now transferred and posted directly or made available to Controlling. New tasks have been assigned to the employees who were involved in the invoice verification process prior to the rollout of the new solution.
Achievement of Goals and Changes Brought About
As a rough estimate, the solution is worthwhile for suppliers who send 10 or more invoices a year. Suppliers who send fewer than 10 invoices may encounter additional costs that cannot be amortized within the duration of depreciation, for example, due to the procurement of a scanner. The aim is to process all invoices electronically. To this end, all suppliers are to submit their invoices electronically in the future via 1stbp. The most significant changes at EDEKA took place at organizational level.
Investments, Profitability, and Key Figures
Costs are incurred by suppliers for printing and enveloping invoices as well as for paper transport and postage costs (approx. EUR 1.80). Costs are incurred by EDEKA for entering (by means of an OCR scanner) and manually processing invoices. The tax liability of these costs must be determined and they must be distributed throughout the Group and recorded in the accounts.
Table 1: Minimum Costs for a Non-Electronic Invoice
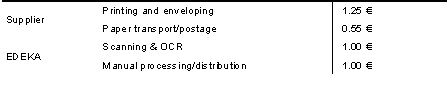
Potential savings for suppliers of more than EUR 0.55 are assumed since the postage costs can be saved at the very least. EDEKA calculates potential savings of at least EUR 1 for each paper invoice. The potential savings shown in Tab. 2 can be achieved if 400,000 of the approximately 440,000 bills of charges sent to EDEKA each year are submitted electronically.
Table 2: Potential Savings for 440,000 Bills of Charges

These potential savings must be compared with the costs for suppliers of no more than EUR 0.28 per invoice and any new Internet costs incurred. The suppliers may also need to buy a scanner so that they can scan any attachments that are relevant for invoicing and send these electronically. At EDEKA, the savings must be compared with the costs for continuous maintenance, which amount to approximately EUR 20,000 a year. This means that at least EUR 180,00 is saved each year at a conservative estimate and EUR 380,000 under optimum conditions. These calculations do not directly take account of the fact that the invoices are now paid much faster (exploitation of cash discount) and that the new process is more transparent.
6. Success Factors
Special Features of the Solution
The innovation in the area of invoice processing at EDEKA is a solution that creates added value for all parties involved. Suppliers can access the 1stbp data at any time to view the status of their invoice and check whether it is correct and has already been processed and made available, or has already been downloaded by EDEKA. Customers of 1stbp can define invoice fields that 1stbp is to verify.
Reflection of "Business Collaboration"
The suppliers and the various organizational units of EDEKA operate at different locations. The new process allows all suppliers to send invoices cost-effectively over the Internet regardless of location. EDEKA also accesses the invoices over the Internet using 1stbp as an intermediary, which results in a transparent process for the suppliers. The time taken for invoices to be paid has been reduced significantly. This is advantageous to the suppliers, since invoices are paid quickly, and to EDEKA, who can exploit its cash discount.
Lessons Learned
Within the scope of a new project, more care would be taken to inform at an earlier stage the specialist departments affected that were not involved in planning the project about the planning and development of a new solution. The rollout of a software solution that significantly simplifies processes, in this case the invoicing process, must also result in organizational changes. At EDEKA, a complex, multi-level, opaque process that involved several organizational units has been transformed into a simple, transparent process involving only a few organizational units.