Konsignationslager zwischen der Röhm GmbH & Co. KG und der BASF Coatings AG
Der Degussa-Geschäftsbereich Röhm stellt Spezialkunststoffe, beispielsweise für die Lackindustrie, her. Zusammen mit BASF Coatings entwickelte Röhm ein erweitertes Vendor Managed Inventory, das neben der Bewirtschaftung eines Konsignationslagers, der aktuellen und exakten Übernahme der Tankfüllungen beim Kunden via Telemetrie, der Übernahme von Vorhersagewerten, der Weitergabe von Qualitätsinformationen zu Chargen auch die elektronische Abrechnung der Lieferungen umfasst. Der frühzeitige Zugriff auf planungsrelevante Daten und Prozessvereinfachungen kompensierten den Mehraufwand für die Lagerbewirtschaft. Der Hauptnutzen wird in der stärkeren Verbindung mit dem Kunden und dessen Prozessen gesehen.
1. Unternehmen
In der Röhm GmbH & Co. KG in Darmstadt hat die Degussa AG ihre Aktivitäten zur Herstellung von Spezialkunststoffen auf der Basis von Methacrylaten zusammengefasst. Aus der Grundsubstanz Methylmethacrylat stellt das Unternehmen insgesamt 50'000 verschiedene Produkte her, von Lackrohstoffen, Reaktionsharzen und Pharmapolymeren bis hin zu Öl-Additiven und verschiedenen PLEXIGLAS® Produkten.
Röhm GmbH & Co. KG
|
|
Gründung | 1907 als "Röhm & Haas" in Esslingen/Neckar |
Firmensitz | Darmstadt |
Branche | Chemische Industrie |
Geschäftsfelder | Methacrylate (z.B. Monomere, PLEXIGLAS®, Öl-Additive, Pharmapolymere, Reaktionsharze und Lackrohstoffe) |
Firmenstruktur | gehört zum Unternehmensbereich Spezialkunststoffe der Degussa-Hüls Gruppe, umfasst 3 Business Units (Spezialacrylate, Methacrylate, Plexiglas)50 Vertriebs- und Produktionsstandorte in Europa, USA, Asien |
Homepage | www.roehm.com |
Umsatz | 2001: ca. 1 Mrd. € |
Mitarbeiter | 4'400 |
Kunden | ca. 10'000 davon 100 mit Potential für Vendor Managed Inventory |
Kooperationsprozess(e) | Supply Chain Management |
Subprozess(e) | Vendor Managed Inventory |
Softwarelösung | SAP R/3 (Module SD, PP, MM, FI, mySAP SCM (SAP APO CLS), mySAP Workplace, Connector Seeburger |
Abbildung 1: Kurzportrait der Röhm GmbH & Co. KG
Herausforderungen im Wettbewerb
Ein kleiner Teilbereich dieser Produktpalette sind sogenannte Monomere, chemische Basisstoffe, die als Rohstoffe für weiter veredelte Produkte dienen. Methacrylatmonomere sind Flüssigprodukte, die im Tank oder als verpackte Ware gelagert werden und die von den Kunden regelmässig und in grosser Menge verarbeitet werden. Auf Grund dieser Eigenschaften sind Monomere für Vendor Managed Inventory Szenarien interessant.
In der Produktgruppe der Methacrylatmonomere ist die BASF Coatings AG ein wesentlicher Kunde von Röhm. Das weltweit tätige Unternehmen stellt unter anderem Lacke und Farben für die Automobilindustrie her.
BASF Coatings AG
|
|
Gründung | 1903 Gründung der Glasurit-Werke Max-Winkelmann am Standort Münster-Hiltrup1965 Übernahme der Glasurit-Werke Max Winkelmann durch die damaligeBadische Anilin- und Sodafabrik AG, der späteren BASF Aktiengesellschaft.Startpunkt des Aufbaus einer Lackgruppe innerhalb der BASF AG. |
Firmensitz | Münster |
Branche | Chemische Industrie |
Geschäftsfelder | Lacke und Farben |
Firmenstruktur | Unternehmensbereich der BASF-Gruppe mit 27 Produktionsstandorten weltweit |
Homepage | http://www.basf-coatings.de |
Umsatz | 2001: 2,3 Mrd. € (+3%) |
Marktanteli | verfügt über eine starke Marktstellung in Europa, Nord- und Südamerika sowie der Region Asien/Pazifik, unter anderem mit eigenen Gesellschaften in Australien, China, Indien, Japan und auf den Philippinen. |
Mitarbeiter | ca.10'000 |
Â
Die Automobilindustrie verlangt von ihren Zulieferern hohe Flexibilität und übt einen hohen Kostendruck aus. Die Zulieferer versuchen auf sinkende Preise und individuellere Anforderungen ihrer Kunden durch die Implementierung effizienter Kooperationsprozesse mit den eigenen Zulieferern zu reagieren. BASF Coatings reorganisierte deshalb die eigenen Beschaffungsprozesse und lud dabei die fünf Kernlieferanten (Röhm, Bayer, BASF, Hoechst und Clariant) zur Mitarbeit ein. Diese Unternehmen treten zwar am Markt als Wettbewerber auf, sind aber keine Alternativlieferanten für die an BASF Coatings gelieferten Produkte.
2. Ausgangssituation
Strategie
Bislang bestand zwischen Röhm und BASF Coatings ein traditionelles Kunden-Lieferanten-Verhältnis mit Terminaufträgen.
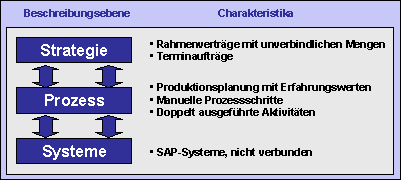
Abbildung 3: Kurzcharakteristik
Prozess
Zu Beginn des Jahres kommunizierte BASF Coatings eine grobe, unverbindliche Bedarfsschätzung. Weitere Informationen über Bedarf und Verbrauch tauschten die Geschäftspartner nicht aus. Die Produktionsplanung bei Röhm beruhte neben diesen Zahlen vor allem auf Erfahrungswerten.
BASF Coatings bestellte via Telefon oder Fax die benötigten Chemikalien. Waren die Chemikalien in ausreichender Menge im Lager, führte Röhm die Bestellung wunschgemäss aus, anderenfalls erhielten die Kunden eine rationierte Abgabemenge. Zusammen mit der Ware wurden Lieferschein und andere Begleitdokumente wie Analysezertifikate und Sicherheitsdatenblatt papierbasiert verschickt. BASF Coatings überprüfte bei Wareneingang jede Lieferung auf die Einhaltung der Qualitätsstandards und lagerte sie anschliessend ein. Für jeden einzelnen Auftrag wurde eine papierbasierte Rechnung erstellt. Einen Überblick über den Prozess liefert Abbildung 4.
Systeme
Röhm tauschte zwar bereits mit anderen Kunden Bestell- und Lieferdaten via EDIFACT (Electronic Data Interchange for Administration, Commerce and Transport) aus, zu BASF Coatings bestand jedoch keine elektronische Schnittstelle. Als Enterprise Ressource Planning (ERP)-System verwendeten beide Unternehmen SAP Produkte. Während bei BASF Coatings bis Juni 2002 noch SAP R/2 im Einsatz war, stand Röhm ein SAP R/3 System zur Verfügung. Die Produktionsplanung bei Röhm wurde durch Microsoft Excel unterstützt und war nicht mit dem ERP-System gekoppelt.
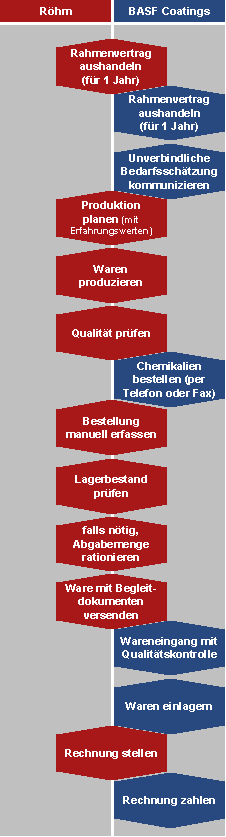
Abbildung 4: bisheriger Prozess
Leidensdruck
Die Zusammenarbeit zwischen Röhm und BASF Coatings war ineffizient:
- Röhm hatte nur ungenaue Informationen über den Bedarf von BASF Coatings. So waren weder Lagerbestand noch kurzfristige Entnahmespitzen bekannt. Die Lieferpläne der Automobilzulieferindustrie, auf deren Grundlage die Lacke mit einer Vorlaufzeit von 2-4 Wochen abgerufen wurden, waren Röhm nicht bekannt. Eine so kurzfristige Produktion der dafür benötigten Lackrohstoffe ist technisch nicht möglich und wäre auch nicht wirtschaftlich. Röhm produzierte die Chemikalie folglich nur auf Grundlage grober Schätzungen auf Lager. Umgekehrt hatte BASF Coatings keine Informationen über Röhm’s Lieferpläne und den jeweiligen Lieferstatus.
- Obwohl alle Kunden von Röhm einen relativ gleichmässigen Bedarf haben, führten Nachfrageschwankungen regelmässig dazu, dass die Lieferungen an die Kunden rationiert werden mussten. Auf beiden Seiten entstanden deshalb hohe Sicherheitsbestände in den Lagern.
- Röhm und BASF Coatings führten viele Arbeitsschritte doppelt aus. Beide überprüften die Qualität der Chemikalien – Röhm nach der Produktion, BASF Coatings bei Wareneingang.
- Der Datenaustausch war telefonisch bzw. papierbasiert mit nachträglicher händischer Dateneingabe in die bestehenden Systeme. Dies führte zu hohen Prozessdurchlaufzeiten.
- Der Kostendruck der Automobilhersteller zwang Zulieferer wie BASF Coatings zur Reorganisation der Beschaffungsprozesse. Dadurch wurde der Kostendruck in der Lieferkette weitergegeben. Röhm hatte die Optimierung seines Unternehmens-Netzwerkes durch Kapazitätsabgleich zwischen Kundenaufträgen und Ressourcen in Echtzeit bereits als IT-Vision definiert.
3. Projekt
Ziele
BASF Coatings initiierte zur Optimierung seiner Einkaufsprozesse das Projekt PROGRESS (process integrated supply) und lud die Kernlieferanten, darunter Röhm, zur Mitwirkung ein. Auf Geschäftsführungsebene vereinbarten beide Unternehmen eine strategische Partnerschaft mit kooperativen Prozessen, um Kosten zu reduzieren, Durchlauf- und Bearbeitungszeiten zu verkürzen sowie Informationsqualität und Servicegrad zu verbessern.
Aus dem politischen Willen des Top Managements wurde zunächst auf Fachebene, später unter Beteiligung der IT-Abteilungen, gemeinsam die Projektdefinition abgeleitet. Die Analyse der gemeinsamen Prozesse zeigte die grössten Nutzenpotentiale in der Realisierung von Konsignationslagern, einer Spezialform von Vendor Managed Inventories (VMI), bei welcher der Lieferant Eigentümer des Lagerbestandes bleibt. Röhm sah darin die Chance, die Kundenbeziehung zur BASF Coatings zu intensivieren. Das Projekt wurde von diesen strategischen Überlegungen geleitet und von engen Terminvorgaben des Top Managements getrieben. Röhm verzichtete auf eine detaillierte Wirtschaftlichkeitsrechnung.
Durchführung
Die strategische Zusammenarbeit wurde im April 2000 vereinbart. Nach der Projektdefinitionsphase wurde das Konsignationslager-Szenario ab 2001 implementiert. Dem Projektteam gehörten auf der Seite der Fachbereiche neben der Projektleiterin, Frau Dr. Scholz, zwei Mitarbeiter des Verkaufs und ein Mitarbeiter der Produktion an, die in Teilzeit insgesamt etwa 20-30 Personentage investierten. Die IT-Projektleitung hatte Edwin Wieland von der Degussa-IT-Tochter its.on[1] inne. Von Seiten der BASF Coatings arbeiteten weitere vier Personen im Konsignationslager-Projekt mit.
Mit der Prozessoptimierung im Auftrag des Geschäftsbereichs waren technische Hürden verbunden. Röhm und BASF Coatings hatten unterschiedliche Systeme im Einsatz. Zudem hatten beide Seiten unterschiedliche Stammdatenstrukturen. So kann einer Chemikalie bei BASF Coatings eine Artikelnummer zugeordnet sein, während Röhm je nach Verpackungsart (z.B. Stoff lose, Stoff verpackt) mehrere Produkte unterscheidet. Hier war die Entwicklung von Mappingmechanismen erforderlich.
Das zentralisierte Know-how in der IT-Abteilung erleichterte dies erheblich. Da die Mitarbeiter u.a. auch mit den Stammdatenstrukturen vertraut waren, entfiel hier eine zeitaufwändige interne Abstimmung mit anderen Abteilungen.
Die professionelle Steuerung des PROGRESS-Projektes der BASF Coatings, unterstützt durch die EDL Consulting, ermöglichte eine schnelle Implementierung des Konsignationsprozesses mit Röhm. Besonders hilfreich waren die von der BASF Coatings organisierte „IT-Roundtables“ mit den Projektleitern aller Kernlieferanten. Der Austausch von Lessons Learned in den jeweiligen Projekten nutzte allen Beteiligten.
Kritische Erfolgsfaktoren
Als wesentlichen Erfolgsfaktor nennt Peter Kühn, Leiter des für Röhm zuständigen Bereichs des IT-Diensleisters its.on, den starken politischen Druck des Top-Managements. Der gemeinsame Wille, die Zusammenarbeit der Unternehmen zu intensivieren und Synergieeffekte zu nutzen, war Ausgangspunkt der Definition eines geeigneten Projektes.
Wichtig ist ein gemeinsames Problemverständnis aller Beteiligten. Notwendige Projekte können jedoch nur zeitnah realisiert werden, wenn zur gemeinsamen Sprache der gemeinsame Lösungswillen hinzutritt. Die Verantwortlichen bei Röhm und BASF Coatings waren entschlossen, die gemeinsamen Nutzenpotentiale eines Konsignationslagers zeitnah zu realisieren. BASF Coatings brachte dazu auch die Erfahrungen vergleichbarer Projekte mit anderen Lieferanten ein.
Gerade VMI-Projekte zeichnen sich durch eine hohe Komplexität aus, für deren Lösung die Projektplanung genügend Zeit vorsehen sollte. Ideale VMI-Projekte sollten nach Einschätzung von Kühn dennoch den Zeitraum von 12 Monaten nicht überschreiten.
4. Neue Lösung
Strategie
Röhm betreibt nun für BASF Coatings Konsignationslager auf deren Werkgelände.
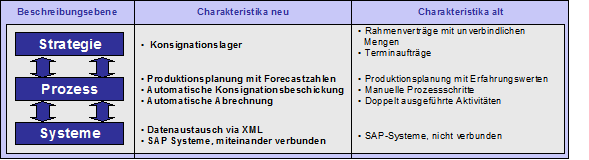
Abbildung 5:Kurzcharakteristik
Prozess
Der Geschäftsbereich Röhm Methacrylate übernimmt die Befüllung der Tanks und die Belieferung mit Fassware auf Basis der von BASF Coatings übermittelten Bestände, Planbedarfe und geplante Entnahmen. Die Chemikalien werden von BASF Coatings bei Entnahme durch Gutschrift („self billing“) bezahlt. Der Austausch von Begleitdokumenten, etwa von Analysezertifikaten, erfolgt zukünftig weitgehend über eine elektronische Plattform.
Einen Überblick über den realisierten Kooperationsprozess liefert Abbildung 6. Die Prozessautomatisierung (Bestands- und Entnahmemessungen, Bedarfsberechnung, Auslösung von Beschickungsaufträgen, Abrechnung) führt dazu, dass die Mitarbeiter mehr Kontrollfunktionen wahrnehmen und weniger aktiv in den Prozess eingreifen als bisher.
Der neue kooperative Prozess zwischen BASF Coatings und Röhm besteht aus vier Subprozessen:
1. „Collaboration“: Röhm erhält monatlich rollierend ein Jahr im voraus die Prognose des Chemikalienbedarfs. Auf Grundlage dieser Informationen werden entsprechende Produktionsmengen berechnet und terminiert.
2. „Consignation“: Die aktuellen Bestände der Silotanks (Flüssigkeiten und Granulate) werden täglich per Telemetriemessung an Röhm übermittelt. Ebenfalls gemeldet werden die kurzfristigen Entnahmen auf Basis freigegebener Fertigungsaufträge der BASF Coatings. Röhm stellt sicher, dass dafür jederzeit ausreichende Bestände in den Konsignationslagern vorhanden sind. Für Stückgut werden die Bestände aus den SAP R/3-Beständen der BASF Coatings rekonstruiert. Eine automatische Verbrauchsmessung für diese Produkte, etwa mit Hilfe von an Paletten befestigten Chips, wurde aus Kostengründen verworfen.
3. „Frozen Period“: Die Transitzeit für die Chemikalien zwischen Röhm und BASF Coatings Werken definiert eine Zeitspanne, in der keine Lieferänderungen mehr möglich sind. Bei Wareneingang prüft BASF Coatings nun nicht mehr die Qualität jeder Lieferung, sondern führt Stichproben auf Basis der jetzt online bereitgestellten Analysezertifikate durch. Aus versicherungstechnischen Gründen werden die Waren bereits jetzt in den Systemen der BASF Coatings verbucht, bleiben aber im Besitz von Röhm. Ausser dem Lieferschein werden in allen Teilprozessen keine papierbasierten Dokumente mehr verschickt.
4. „Settlement“: Die täglich übermittelten Entnahmebuchungen der BASF Coatings führen zur Buchung entsprechender Konsignationsentnahmen bei Röhm. Der Rechnungsversand entfällt, da so beide Partner die gleichen Entnahmemengen zugrundelegen. Die Zahlungen von BASF Coatings werden nun einfach gegen eine systemintern erstellte Monatsrechnung gebucht.
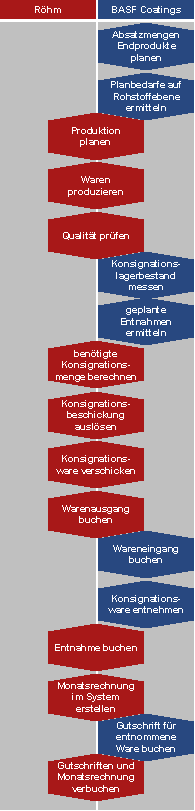
Abbildung 6: neuer Prozess
System
Im Rahmen des implementierten Kooperationsprozesses setzen beide Partner SAP R/3 ein. Der SAP APO (Advanced Planning Optimizer) unterstützt die Produktionsplanung auf Grundlage der rollierenden 12-Monats-Forecasts (sog. Monatstableau) und die Konsignationsbeschickung über die Entnahmemeldungen (sog. Tagestableu). Der SAP Workplace visualisiert die übermittelten Plan-, Bestands- und Entnahmedaten und stellt Begleitdokumente elektronisch bereit. Abbildung 7 illustriert die zugrundeliegende Systemarchitektur.
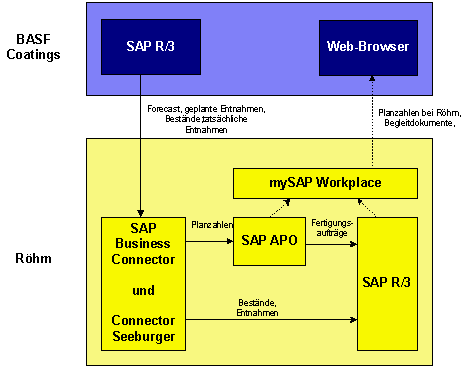
Abbildung 7: Systemarchitektur
Plan-, Bestands- und Entnahmeinformationen werden im XML-Format versandt und bei Röhm über den SAP Business Connector bzw. Connector Seeburger angenommen und verarbeitet. Dafür nutzen die Partner Teile des auf XML aufsetzenden Standards Chemical Industry Data Exchange (CIDX), der Prozesse und auszutauschende Daten für die chemische Industrie definiert [www.cidx.org]. Das von Röhm verwendete Derivat besteht nur aus den im konkreten Fall benötigten Felddefinitionen (s. Abbildung 8).
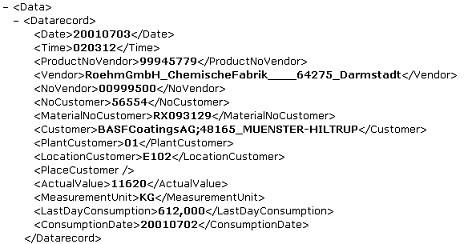
Abbildung 8: Beispiel einer XML-Nachricht zwischen Röhm und BASF Coatings
Bei der Systemauswahl orientierten sich die Partner konsequent an der jeweils vorhandenen Applikationslandschaft mit ERP-Systemen auf SAP-Basis. Für die Produktionsplanung setzt Röhm deshalb SAP APO ein; der Zugriff auf Informationen aus den SAP-Systemen von Röhm wird über SAP Workplace ermöglicht. Hier gehen die Verantwortlichen mittelfristig von einer Migration auf das Nachfolgeprodukt SAP Portals aus.
Kosten und Nutzen
Das Konsignationslager-Szenario wurde ab Januar 2001 für ein Produkt in Betrieb genommen, im Juni 2001 kam ein weiteres Produkt hinzu. Seit Oktober 2001 werden sämtliche innerdeutschen Lieferungen von Röhm an BASF Coatings mit Hilfe des unternehmensübergreifenden Prozesses abgewickelt. Weitere Roll-outs für die europäischen Standorte der BASF-Coatings sind in der Umsetzungsphase. Eine Übertragung der Lösungselemente auf andere Kunden ist in Vorbereitung.
Die Implementierung des Konsignationsprozesses hat zu einer engeren Zusammenarbeit zwischen der Röhm GmbH & Co. KG und dem strategisch wichtigen Kunden BASF Coatings AG geführt. Beide Partner reduzieren Prozesskosten und -durchlaufzeiten.
Röhm kann seine Monomerproduktion genauer planen und die Konsignationslager bei der BASF Coatings automatisiert nachfüllen. Der elektronische Dokumentenaustausch ersetzt den papierbasierten Austausch. Durch den neuen Abrechnungsprozess entfällt zudem die Rechnungsprüfung.
BASF Coatings bindet durch die Konsignation künftig kein Kapital mehr in Sicherheitsbeständen für Monomere, kann die Prozessschritte Bestellung und Qualitätsprüfung einsparen und die Abrechnung vereinfachen.
Die Partner errechneten ein gemeinsames Einsparvolumen von 500'000 € jährlich, wovon bisher 100'000 € pro Jahr allein im Bereich der Prozesskosten eingespart werden konnten. Eine Übersicht über realisierte Nutzenpotentiale liefert Abbbildung 9.
Der neu implementierte Konsignationsprozess involviert bei Röhm etwa fünf Mitarbeiter direkt (zwei Mitarbeiter im Verkauf, zwei Mitarbeiter in der Produktion und etwa einen Mitarbeiter in der Buchhaltung). Das System wurde von ihnen anfänglich sehr gut aufgenommen. Da die Zusammenarbeit mit BASF Coatings Pilotcharakter hat, müssen die Mitarbeiter jedoch zwei Prozesse bedienen. Alle anderen Kunden bestellen derzeit weiter mit Terminaufträgen. Dies führte dazu, das auch für die Zusammenarbeit mit BASF Coatings teilweise auch die alten Kanäle (Telefon und Fax) wieder genutzt wurden, bis dies von der Führung explizit untersagt wurde. Die genannten Nutzenpotentiale für Röhm werden deshalb wohl mittel- bis langfristig nur dann realistisch sein, wenn es gelingt, einen möglichst grossen Umsatzanteil über Konsignationsprozesse abzuwickeln.
Geplante Weiterentwicklungen
Es wurde bereits begonnen, vergleichbare VMI-Szenarien zusammen mit anderen Kunden zu realisieren. Eine einfache Übertragung des zwischen Röhm und BASF Coatings implementierten Prozesses ist jedoch nicht möglich, da die Komplexität des Prozesses und die unterschiedlichen prozess- und systemtechnischen Voraussetzungen der Kunden zwangsläufig zu anderen Prozessvarianten führen werden. Der Pilotprozess und die Projektmethodik eignen sich jedoch als Muster, das insbesondere dort grösstenteils übernommen werden kann, wo die Kunden noch keine eigenen Vorstellungen von einem VMI-Szenario entwickelt haben.
Dennoch sehen Peter Kühn und Edwin Wieland die Zukunft von m:n-fähigen Marktplätzen im VMI-Bereich derzeit kritisch, da diese den kundenspezifischen Zuschnitt der Prozesse nicht unterstützten können. Bei Röhm selbst wurde ein Marktplatz bisher nur in wenigen Fällen eingesetzt. Dabei handelte es sich jedoch nur um einen einfachen Order/Invoice-Prozess, bei dem Bestellfax und schriftliche Rechnung durch elektronische Dokumente abgelöst wurden.
Überblick VMI-SZENARIO ZWISCHEN RÖHM UND BASF COATINGS
|
|
Aufwand: | |
Projekt | |
Laufzeit | April 2000 – Oktober 2001 |
Projektteam
|
|
Projektaufwand (Personentage)
|
|
Projektkosten | 200'000 € |
Hard- und Softwarekosten | ca. 50'000 |
Durch das VMI-Szenario realisierte Potenziale: | |
Finanzen | |
Gemeinsames Einsparvolumen insgesamt | 500'000 € |
|
100'000 € |
Kunden | |
Verbesserte Kundenbindung | Erreicht, durch Konsignationslager |
Prozesse | |
Verkürzung der Prozesszeiten | Erreicht, durch Automatisierung und Einsparung von Prozessschritten |
Â
5. Erkenntnisse
Das Beispiel des Geschäftsbereichs Röhm Methacrylate illustriert die Potentiale, die Unternehmen durch enge, IT-gestützte Kooperationen erzielen können. Röhm und BASF Coatings verbessern die Prozessqualität durch die zeitnahe, automatisierte Übermittlung von Dispositionsinformationen und reduzieren das in Lagerbeständen gebundene Kapital. Die automatisierte Übermittlung und Verarbeitung von Plan-, Bestands- und Entnahmedaten verkürzt die Reaktionszeit von Röhm im Vergleich zur bisher üblichen telefonischen Bestellung durch BASF Coatings.
Das Redesign der Prozesse (z.B. Übertragung der Lagerverantwortung an den Lieferanten, automatische Leistungsverrechnung, elektronische Dokumentation), führt zu einer Prozesskostensenkung.
Der kooperative Prozess zwischen Röhm und BASF Coatings ist exakt auf die Besonderheiten der beiden Unternehmen abgestimmt. Dadurch kann Röhm für BASF Coatings Zusatznutzen stiften, den andere Wettbewerber nicht liefern können. Im konkreten Fall äussert sich dieser Zusatznutzen in der Übernahme der Verantwortung für einen ausreichenden Rohstoffbestand beim Kunden.
Die Realisierung eines Konsignations-Szenarios führt zu einer engeren Zusammenarbeit zwischen dem Geschäftsbereich Röhm Methacrylate und BASF Coatings mit automatisiertem Datenaustausch und massgeschneiderten Prozessen. Eine derart enge Bindung schafft auch dem Lieferanten Nutzen, da sie die Kosten für einen Lieferantenwechsel des Kunden erhöht.
- Der Kunde BASF Coatings betrieb gleichzeitig ähnliche Projekte mit weiteren Zulieferern. Da sich die Zulieferer bei BASF Coatings nicht konkurrieren, konnte BASF Coatings einen Erfahrungsaustausch organisieren, der allen Projekten zugute kam.
- Die Partner rechneten Kosten und Nutzen des Projektes nicht gegeneinander auf. Röhm und BASF Coatings wollten ihre Zusammenarbeit nicht durch das gegenseitige Aufrechnen von Kosten und Nutzen belasten. Die Einsparpotentiale des VMI-Szenarios wurden für die Kooperationsbeziehung insgesamt evaluiert. Jedes Unternehmen trug seinen Aufwand selbst und rechnet damit, dass dieser durch den erzielten Nutzen gerechtfertigt ist.
[1] Die Degussa-Hüls Gruppe legte zum 1.1.2002 die Informatikaktivitäten der einzelnen Tochtergesellschaften im IT-Dienstleister its.on GmbH & Co. KG mit insgesamt ca. 750 Mitarbeitern zusammen. Die Zuständigkeiten für einzelne Projekte änderten sich dadurch nicht.