Ersatzteilmanagement bei der AMAG Automobil- und Motoren AG
Die AMAG, der schweizerische Importeur von Volkswagen, reorganisierte ihren Prozess der Ersatzteilversorgung durch eine neue Form der Zusammenarbeit zwischen Volkswagen, AMAG Zentrallager, AMAG Regionallager und Kraftfahrzeugwerkstätten (Garagisten). Von der Ersatzteilbestellung des Garagisten über die Nachbevorratung aus dem Volkswagen Ersatzteillager in Kassel und von anderen Lieferanten, über den Schweizer Zoll, die Lagerbestände und -orte im Zentral- und den Regionallagern bis zur Auslieferung an den Garagisten greift der gesamte Prozess in Echtzeit auf die gleiche Datenbasis zu. Damit kann die AMAG mittelfristig eine bestehende Handels- und Lagerstufe auflösen und die rasch wachsende Komplexität der Ersatzeillogistik aufgrund schneller Modellwechsel und Variantenvielfalt bewältigen. Sie realisiert zudem eine zentrale Anlaufstelle für den Kunden („One-face-to-the-customer“) anstelle einer Produktgruppenzuständigkeit in der Vergangenheit.
1. Unternehmen
Überblick
Die Automobil- und Motoren AG (AMAG) ist der Schweizer Generalimporteur für die Marken des Volkswagen-Konzerns (VW, Audi, Seat, Skoda) und Fahrzeuge der Dr. Ing. h.c. F. Porsche AG. Von der AMAG wird ein Bestand von 750'000 Fahrzeugen betreut. Der grösste Teil davon sind Personenwagen der Marke VW.
AMAG Automobil- und Motoren AG
|
|
Gründung | 1945 |
Firmensitz | Zürich |
Branche | Automobilgewerbe |
Geschäftsfelder | Automobil-Import/Handel, Ersatzteilhandel, Leasing |
Firmenstruktur | Gehört zur AMAG Gruppe, die weitere Aktivitäten im Automobilsektor (u.a. Autovermietung, Parkhäuser in eigenen Gesellschaften zusammengefasst hat) |
Homepage | http://www.amag.ch |
 | |
Umsatz | 2002: 3'300 Mio. CHF |
Ergebnis | k. A. |
Marktanteil | Automobilhandel: 20% (2002) |
Mitarbeiter | 3'342 (inkl. Filialbetriebe) |
Kunden | Ersatzteilgeschäft : > 10'000 Kunden |
 | |
Kooperationsprozess(e) | Reparatur & Instandhaltung |
Subprozess(e) | Ersatzteilmanagement |
Softwarelösung | SAP ET 2000 (von VW angepasstes SAP R/3 mit den Modulen SD, MM, WM), Lagerabwicklung mit LAPS (Eigenentwicklung) |
Â
Herausforderung im Wettbewerb
Zum Fahrzeugbesitz gehört dessen regelmässige Reparatur und Wartung und damit der Austausch von defekten Teilen. Die Verfügbarkeit von Ersatzteilen beeinflusst die Reparaturzeiten und damit den Nutzen des Fahrzeugs für den Kunden sowie die Reputation der Marke. Der Verkauf von Neuwagen beinhaltet die Verpflichtung, Ersatzteile für die Fahrzeuge bereitzustellen. Für die Marken des VW-Konzerns sind für die Fahrbereitschaft wichtige Ersatzteile bis mindestens 15 Jahre nach Ende der Serienproduktion des Fahrzeugtyps erhältlich.
Das Zentralersatzteillager der AMAG für die vertretenen Marken befindet sich in Buchs (ZH) und ist seit 1957 auf 40'000 Quadratmeter Fläche gewachsen. In dem organisch gewachsenen Lager, das von manueller Lagertechnik dominiert wird, werden durchschnittlich 150'000 Lagerpositionen gehalten – von Reifen und Stossstangen über Spezialwerkzeuge zur Fahrzeugreparatur bis zu Boutique-Artikeln wie VW-Uhren oder Porsche-Schlüsselanhänger. Insgesamt sind über 600'000 Artikel gelistet.
Die Komplexität der Lagerhaltung hat in den letzten Jahren und Jahrzehnten konstant zugenommen. So stieg die Anzahl der Fahrzeugtypen, während sich gleichzeitig die Produktionsdauer einer Serie drastisch verkürzte. In Folge müssen immer mehr Ersatzteile vorgehalten werden. Herausforderung des Ersatzteilgeschäfts ist das Management dieser Komplexität und die Sicherstellung der Lieferfähigkeit. Masszahl dafür ist der Servicegrad, d.h. der Anteil der Bestellungen, die sofort befriedigt werden können.
2. Ausgangssituation
Abbildung 2: Kurzcharakteristik
Strategie
Die AMAG hatte ein zweistufiges Ersatzteilvertriebssystem. Das Zentrallager in Buchs (ZH) belieferte 36 Auslieferungslager in der ganzen Schweiz. Diese belieferten die Autowerkstätten ihres Marktverantwortungs-Gebietes. Das Zentrallager selbst war nach produktorientierten Fachbereichen organisiert und bezog die Ersatzteile direkt von den Herstellern VW und Porsche.
Prozess
Drei wesentliche Prozesse des Ersatzteilmanagements sind die Bestellabwicklung, der Wareneingang und die Kommissionierung. Bei der AMAG fand die Bestellabwicklung mehrstufig statt. Kunden bezogen ihre Ersatzteile vom Auslieferungslager. Für die Bevorratung bestellten die Auslieferungslager beim Zentrallager, welches wiederum bei den Herstellern Ersatzteile bestellte. Abbildung 2 2 illustriert die bisherige Ersatzteilabwicklung der AMAG mit Fokus auf die Bestellabwicklung:
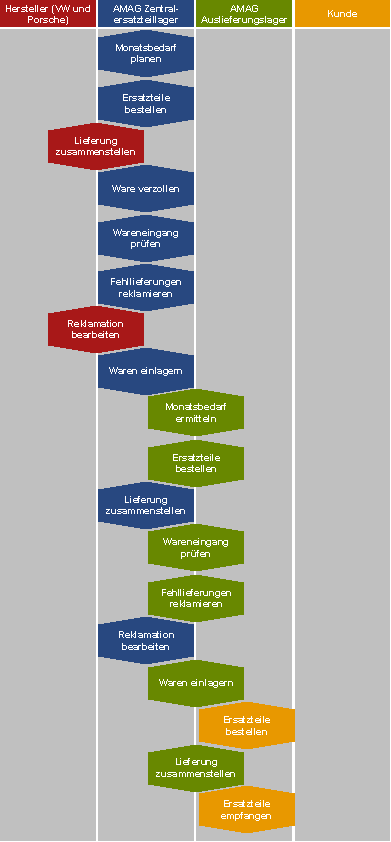
Abbildung 3: Bisheriger Prozess
1. Bestellungen der Auslieferungslager:
Die Auslieferungslager bestellten monatlich ihren Bedarf im Zentrallager. Die manuelle Ermittlung des Bedarfs und Erstellung der Bestellung nahm durchschnittlich 1-2 Tage in Anspruch. Das Zentrallager stellte die bereitgestellten Teile zusammen und lieferte sie an das Auslieferungslager. Diese Lieferungen umfassten meist mehr als 2000 Positionen. Die Wareneingangskontrolle, die jede Position einzeln überprüfte, stellte deshalb häufig Abweichungen von der Bestellung fest. Ein aufwendiger Reklamationsprozess war die Folge.
2. Bestellabwicklung mit VW und Porsche:
Die Bestellabwicklung zwischen Zentrallager und VW bzw. Porsche war in einem vergleichbaren Prozess organisiert. Wareneingang: Die Zollabfertigung bestimmte den Wareneingang im Zentrallager. Die Waren durften erst nach zolltechnischer Behandlung entladen und eingelagert werden.
3. Lagerabwicklung (Kommissionierung):
Im Zentrallager fand eine auftragsbezogene Kommissionierung statt. Das bedeutete, ein Mitarbeiter fertigte jeweils einen Auftrag ab und entnahm die bestellten Teile wegeoptimiert aus dem Lager.
Systeme
Die AMAG setzte ein eigenentwickeltes System zur Unterstützung des Ersatzteilgeschäfts ein.
Leidensdruck
- Die produktorientierte Organisation des Ersatzteillagers hatte zur Folge, dass die Kunden bei Bestellvorgängen mehrere Verantwortliche kontaktieren mussten. Eine ganzheitliche Betreuung der Kunden war so nicht möglich.
- Die starre Trennung der Handelsstufen Import und Grosshandel war für die Bewältigung der zunehmenden Komplexität ebenso wenig geeignet, wie die manuellen Bestellvorgänge.
- Zunehmende Sortimentsvielfalt und Teilegrössen (z.B. Karosserieteile) führten zu Platzproblemen im Zentrallager und den Regionallagern.
- Das recht flexible proprietäre Lagerhaltungssystem der AMAG hatte einen limitierten Kundenstamm. Es war absehbar, dass die begonnene Zusammenfassung von Lagern mit dem System nicht abgeschlossen werden konnte, da nach der Reorganisation eine deutlich grössere Anzahl Kunden zu verwalten war. Zudem behinderten Schnittstellenprobleme die Kommunikation mit den Herstellern.
- Verzögerungen in der Zollabfertigung führten zu hohen Kapazitätsschwankungen. Die verplombten Waggons mit den Ersatzteilen aus Deutschland stauten sich am Wareneingang. Dies führte zu hohen Standgebühren von mehreren 10'000 CHF pro Monat und verlängerte die Lieferzeiten.
- Die auftragsbezogene Kommissionierung führte mit zunehmender Lagergrösse zu immer längeren Wegezeiten bei der Zusammenstellung der Aufträge. Die zunehmende Anzahl von Aufträgen erhöhte den Verkehr im Lager und führte dazu, dass sich die Mitarbeiter gegenseitig behinderten.
3. Projekt
Ziele
Wegen des Leidensdrucks im Ersatzteilgeschäft suchte die AMAG nach einer Organisation des Ersatzteilgeschäftes, die trotz zunehmender Komplexität ein Halten des Servicegrades ermöglichte. Dazu gehörte für die AMAG eine höhere Prozesstransparenz, die effiziente Anbindung an die Hersteller und eine Neugestaltung der eigenen Vertriebsstruktur. Die AMAG entschied sich, das Ersatzteilgeschäft organisatorisch umzugestalten und systemtechnisch zu unterstützen.
Seit dem 1998 hatte die AMAG ein SAP R/3 System mit den Modulen Finance (FI), Controlling (CO) und Human Ressources (HR) in Betrieb. Von einer Ausdehnung des R/3-Systems auf andere Geschäftsprozesse erwartete die AMAG Kosteneinsparungen und Prozessverbesserungen durch die Nutzung eines integrierten Informationssystems mit gemeinsamen Stammdaten und Schnittstellen zwischen den einzelnen Modulen.
Der Softwareentscheid wurde dadurch erleichtert, das auch VW im zentralen Ersatzteilwerk in Baunatal und in den deutschen Vertriebszentren SAP-Software einsetzte. Die AMAG beschloss in enger Verknüpfung mit dem VW-Ersatzteilprojekt, die dort aus den Modulen Sales und Distribution (SD), Materials Management (MM) und Warehouse Management (WM) entwickelte Lösung SAP ET 2000 zu übernehmen. Die AMAG entschied sich, ihre Prozesse, wo immer möglich, dem SAP-Standard anzupassen, um den Aufwand bei Softwarereleases zu minimieren.
Durchführung
Das Ersatzteilmanagementprojekt wurde von der Geschäftsleitung intensiv gefördert. Hanspeter Soland, Geschäftsleitungsmitglied für Finanzverwaltung und Informatik, und Rudolf Bernhard, Geschäftsleitungsmitglied Teile und Zubehör und Verantwortlicher für das AMAG-Zentralersatzteillager, waren an der Lenkung des Projektes massgeblich beteiligt.
Das Projektteam bestand neben den beiden internen Projektleitern, Dr. Ursula Kloss (Informatik) und Heinrich Lienhard (Teile und Zubehör), aus 40-60 Mitarbeitern aus Informatik und Fachabteilungen, die ganz oder teilweise in das Projekt eingebunden waren. Die Teilprojekte wurden jeweils von einem Fachverantwortlichen und einem Vertreter der an der Implementierung beteiligten Unternehmensberatung IMG AG geleitet.
In zwei Projektphasen wurde ab Herbst 1998 zunächst der „Proof of Concept“ in den Artikelgruppen Boutique, Industrieartikel und Spezialwerkzeuge erbracht. Systembedingte Lieferverzögerungen waren hier weniger kritisch und auftretende Fehler konnten wegen der relativ kleinen Mengen einfach behoben werden. Nach Einführung der Lösung für diese Nebenverkaufsprodukte im Oktober 1999 konnten erste Erfahrungen gesammelt werden, die in Phase zwei direkt in die Umstellung des Kerngeschäfts einfliessen konnten. Die AMAG berücksichtigte bereits geplante Nachfolgeprojekte im Zusammenhang mit der Reorganisation des Ersatzteilgeschäftes, wie die Integration der Regionallager, und stimmte die Konzeption des Ersatzteilmanagementprojektes darauf ab. Bis zum Abschluss des Projektes am 5. Juni 2000 wurden insgesamt 2000 Personentage aufgewandt.
Die Zusammenarbeit mit VW war eine besondere Herausforderung im Projekt. Das Abstimmen der Interessen und das Warten auf den Abschluss von Vorarbeiten bei VW führten zu Verzögerungen. Der Projektstart begann mit einer längeren Anlaufphase. Für den wichtigen Know-how Transfer delegierte die AMAG zwei Mitarbeiter in das VW-Ersatzteilprojekt, die intensiv an der Erstellung des Deutschlandpiloten in München und des Auslandspiloten in Schweden mitarbeiteten. Das erklärte Ziel der AMAG, möglichst deckungsgleich mit dem SAP Standard zu sein, konnte durch die Vielzahl von Änderungen, die VW im ersten Release (3.1) am SAP Standard vornahm, nicht vollumfänglich erfüllt werden. Mit dem sich im Roll-out befindlichen Release SAP 4.6c haben sich die Partner jedoch wieder stärker dem SAP Standard angenähert.
Kritische Erfolgsfaktoren
Neben der Zusammenarbeit mit VW, die eine hohe Schnittstellenkompatibilität auf Prozess- und Systemebene sicherstellte, sieht Rudolf Bernhard insbesondere die Einbindung des Fachbereichs in das Projekt als kritischen Erfolgsfaktor an. Eine gute Mischung von Fach- und IT-Experten fördert den Wissenstransfer im Projektteam. So können die Systemkenntnisse der Berater und das Wissen des Fachbereichs über die Abläufe zusammengeführt werden. Voraussetzung dafür ist, dass die Schlüsselpersonen mit dem benötigten Überblick über die fachliche Komplexität identifiziert und in das Projekt eingebunden werden. Ein gemeinsamer physischer Projektraum erwies sich als wichtig für die Entstehung des Teamzusammenhalts. Ein gemeinsames Problemverständnis und gute informelle Beziehungen sind für Rudolf Bernhard und Dr. Ursula Kloss die Basis für ein erfolgreiches Projekt, denn „schönste Formalismen nützen nichts, wenn die Leute nicht miteinander reden können“.
Ein weiterer wichtiger Faktor ist das Engagement der Geschäftsleitung für das Projekt. Notwendig sind kurze Entscheidungswege und die Fähigkeit, Entscheidungen schnell und unter Unsicherheit zu fällen, selbst wenn dadurch später Korrekturen notwendig werden. Die Projektleitung führte deshalb wöchentliche Projektsitzungen durch, bei Bedarf auch kurzfristiger.
Die Kommunikation an Mitarbeiter und Kunden ist ein weiterer kritischer Erfolgsfaktor. Die Geschäftspartner wurden frühzeitig über das Projekt und seine Ziele informiert und auf die damit einhergehenden Veränderungen geschult. Die Mitarbeiter erhielten zunächst wöchentlich ein schriftliches Bulletin. Es zeigte sich jedoch, dass eine halbjährliche Information im Rahmen der regulären Informationsveranstaltungen für Mitarbeiter ausreichend ist.
Die Motivation der Projektmitarbeiter setzt hingegen nicht nur eine intensive Kommunikation voraus, sondern erfordert auch das Aufzeigen von Entwicklungsperspektiven. Mitarbeiter, die sich im Projekt zu Know-how Trägern entwickelten, werden bei Interesse und nach Möglichkeit auch in weiteren Projekten eingesetzt. Einige Projektmitarbeiter wechselten aus dem Fach- in den Informatikbereich, da sie dort persönlich ein neues Betätigungsfeld sahen. Die Doppelbelastung durch Projekt- und Tagesgeschäft hält Rudolf Bernhard für unvermeidlich, wenn Kompetenzträger im Projekt mitarbeiten sollen. Zur teilweisen Entlastung der Projektmitarbeiter im Tagesgeschäft verzichtete die AMAG jedoch auf einige Aktivitäten und nahm Verzögerungen im Ablauf administrativer Prozesse bewusst in Kauf.
4. Neue Lösung
Strategie
Die AMAG hat ihren Ersatzteilvertrieb prozessorientiert umgestaltet. Die 36 Auslieferungslager waren bereits in fünf Regionallager zusammengefasst worden. Das Zentrallager übernimmt für die Ostschweiz auch die Rolle des Regionallagers und beliefert Händler, Werkstätten und Endkunden direkt. Eine Zusammenführung der Importstufe (Zentrallager) und der Grosshandelsstufe (Regionallager) findet derzeit statt. Die fünf Regionallager werden damit zu Aussenstellen des Zentrallagers, welches Personal- und Budgetverantwortung übernimmt. Das Regionallager Luzern ist bereits seit dem 1.1.2002 organisatorisch und systemtechnisch in das Zentrallager eingegliedert. Warenbewegungen werden damit zu Umlagerungen und lösen keine internen Bestellvorgänge und Fakturierungen aus.
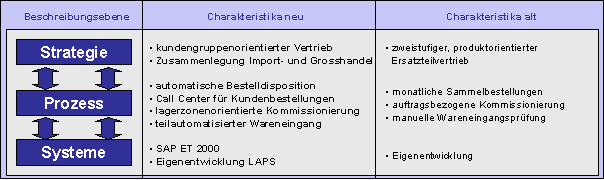
Abbildung 4: Vergleichende Kurzcharakteristik
Die Ersatzteilbestellungen werden zweimal täglich mit einem eigenen Lieferdienst (Gesamtschweizerisch rund 90 Fahrzeuge) den Händlern und Werkstätten geliefert. Das bisher produktorientierte Ersatzteilmanagement löste die AMAG durch eine prozessorientierte Organisation. Als Schnittsstelle zu den Kunden fungiert ein Call Center.
Prozess
Die Reorganisation des Ersatzteilgeschäftes betraf die Bestellabwicklung, den Wareneingang und die Lagerabwicklung (Kommissionierung).
1. Abwicklung von Kundenbestellungen:
Ein zentrales Call Center wickelt die Kundenaufträge ab. Etwa 40 Prozent aller Bestellungen werden innerhalb der sogenannten „Rush Hour“ von 8.30 Uhr bis 11.00 Uhr aufgegeben. Die Waren werden zweimal am Tag an die Händler geliefert. Dies hat Kapazitätsspitzen vor den Auflieferungszeitpunkten zur Folge. Ein Prozess, der diese Kapazitätsspitzen automatisiert abarbeitet, stellt hohe Anforderungen an die Systemressourcen, die ausserhalb der Spitzenzeiten nicht genutzt werden. Die AMAG entschied sich deshalb, manuelle und automatisierte Prozessschritte so zu kombinieren, dass Belastungsspitzen durch menschliche Arbeitskraft abgefangen werden können.
2. Bestellabwicklung mit VW und Porsche:
Die Integration von Zentrallager und Regionallagern erlaubt eine zentrale Warendisposition und Fakturierung. Die Bestellungen zu VW und Porsche laufen automatisiert. Ein automatisches Dispositionssystem löst die manuelle Disposition ab, die durch die zunehmende Komplexität des Ersatzteilgeschäfts immer schwieriger geworden war. Die automatische Bestellung berücksichtigt neben dem Lagerbestand kritische Mengen, Saisonalität (z.B. bei Karosserieteilen) und Lebenszyklus der Autoserien.
3. Wareneingang:
Die AMAG registiert die angelieferten Ersatzteile mit einem Barcode-Scanner und gleicht die aufgenommenen Mengen mit dem Lieferschein ab. Die Wareneingänge können nicht automatisch gebucht werden, da die Lieferung zunächst verzollt werden muss. Die Zollbehörde hat der AMAG inzwischen die Erlaubnis erteilt, die Verzollung mit speziell geschulten Arbeitskräften selbst vorzunehmen (Status: „Zugelassener Empfänger“). Ein Grund dafür ist auch die bessere Nachvollziehbarkeit der Warenbewegungen durch das neue Ersatzteilmanagementsystem. Die früher regelmässigen Stillstände am Wareneingang treten jetzt nur noch bei den sporadischen Inspektionen durch den schweizerischen Zoll auf. Die Einbuchung der Bestände (und damit die Sichtbarkeit im Lager) erfolgt innerhalb weniger Stunden. Die Zollproblematik verhindert derzeit noch eine Verbuchung in Echtzeit.
4. Kommissionierung:
Das Zentrallager selbst ist neu in 22 Lagerzonen aufgeteilt. Aufträge werden nun in diese Lagerzonen geteilt. Im Extremfall stellen 22 Mitarbeiter gleichzeitig eine Lieferung zusammen. Der Auftrag wird in der Warenausgangszone zusammengeführt. Die einzelnen Aufträge werden nach Kunde und Tour sortiert. Die Fahrer können die Vollständigkeit ihrer Touren durch strichcodebasierte Auslieferungslisten überprüfen.
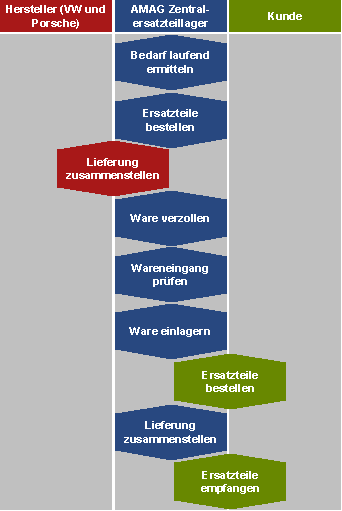
Abbildung 5: Neuer Prozess
Systeme
Die neue Ersatzteillösung kombiniert SAP ET 2000 mit dem selbstentwickelten Kommissionierungssystem LAPS (Lagerabwicklungs- und Planungssystem). Eine Übersicht über die Systemarchitektur liefert Abbildung 6.
Mit SAP ET 2000 realisiert die AMAG die Auftragsbearbeitung. Die im System abgebildeten Prozesse entsprechen, gemäss den Projektvorgaben, wo immer möglich den von SAP bzw. VW gesetzten Standards. Sonderlösungen existieren für die (im VW-System nicht erforderliche) Zollabwicklung und die im Vergleich zum Standard vereinfachte Wareneingangsabwicklung. Das Privatkundengeschäft und die Integration von Regionallagern waren in den Standards ebenfalls nicht vorgesehen, so dass auch hier eigene Weiterentwicklungen, wie z.B. die Implementierung einer Kreditkartenabrechung, erforderlich waren. Hinzu kamen die Unterstützung von drei Schweizer Landessprachen (Deutsch, Französisch und Italienisch) mit entsprechenden Formularen sowie AMAG-spezifische Auswertungen.
Mit dem integrierten Dispositionssystem (IDIS) kommt eine von VW entwickelte Zusatzkomponente des SAP ET 2000 zum Einsatz, die den automatischen Warennachschub ermöglicht. Zweimal täglich gehen Bestellungen an VW bzw. erhält AMAG Rechnungs- und Lieferdaten von VW. Die im IDOC-Format ausgetauschten Datensätze enthalten u.a. Bestellnummer, Menge, Materialnummer und Preis. Eine ähnliche Komponente entwickelte die AMAG für die Bestellung bei Porsche [1] .
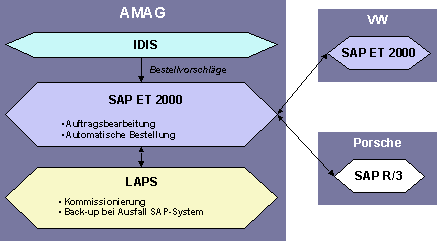
Abbildung 6: Systemarchitektur
Das Management der physischen Warenbewegungen wird durch LAPS gesteuert. Dazu gehört die Aufteilung des Lieferauftrags auf die 22 Lagerzonen und der Druck der Strichcode-Labels. Die Aufträge werden dazu laufend aus SAP ET 2000 über das IDOC-Format in LAPS übertragen und nach Erledigung wieder in das ET-System zurück. Für die im LAPS integrierte Notfallfunktion (Ausfall SAP ET 2000) werden die Teilebestände nachts mit SAP ET 2000 abgeglichen. Zwar können keine Wareneingänge im LAPS gebucht werden, die Kommissionierung auf Basis des letzten Datenabgleichs ist aber trotzdem möglich. Ist das SAP ET 2000-System nicht verfügbar (etwa bei Inventuren oder Systemausfall) können am ersten Tag 90 Prozent des üblichen Auftragsvolumens abgewickelt werden, am dritten Tag immerhin noch 70 Prozent.
Kosten und Nutzen
Der AMAG gelang es mit der Umstellung ihres Ersatzteilmanagements und der Implementierung kooperativer Prozesse mit VW und Porsche, den Servicegrad trotz zunehmender Teilevielfalt zu halten. Die Reorganisation des Ersatzteilvertriebs und die erhöhte Prozesstransparenz erlaubten der AMAG zudem, die Sicherheitsbestände pro Lagerposition zu reduzieren. Eine verbesserte Zollabfertigung spart jährlich bis zu 200'000 CHF an Standgebühren ein.
Die Einführung des neuen Lagermanagementsystems aus SAP ET 2000 und LAPS führte zu einer drastischen Reduktion des Änderungsaufwands der Applikation. Während beim Betrieb des Altsystems ständig etwa 20 Änderungsanträge mit grossem Arbeitsaufwand anhängig waren, ermöglicht der Einsatz der Standardsoftware vereinfachte Anpassungen durch Customizing und erlaubt einen grösseren Spielraum für die weitere Entwicklung.
Die Implementierung der neuen Lösung erforderte einen Arbeitsaufwand von insgesamt 2'000 Personentagen. Die Gesamtkosten (ohne den Arbeitsaufwand der AMAG-Mitarbeiter) beliefen sich auf 5-6 Mio. CHF. In der Fachabteilung Informatik betreuen vier Personen das ET-System; ca. 20% ihrer Arbeitszeit ist für Support und kleinere Korrekuren/Verbesserungen erforderlich. Die übrige Zeit wird für Weiterentwicklungen sowie neue Projekte verwendet. Eine Übersicht über Kosten und Nutzen des AMAG Ersatzteilmanagementprojekts liefert Abbildung 7.
Überblick AMAG Ersatzteilmanagement
|
|
Aufwand: | |
Projekt | Â |
Laufzeit
|
20 Monate
|
Projektteam
|
40-60 Personen
|
Projektaufwand (Personentage) | 2'000 PT |
Projektkosten (ohne Arbeitszeit der AMAG Mitarbeiter) | 5-6 Mio. CHF |
Softwarekosten | 1,6 Mio. CHF |
Betrieb | Â |
Tagessupport und Kleinstanforderungen | 1 Mitarbeiter |
SAP Basis / Operating / Netzwerk | 1-2 Mitarbeiter |
Durch die Reorganisation des Ersatzeilmangements realisierte Potenziale: | |
Finanzen | Â |
Reduzierte Sicherheitsbestände pro Lagerposition | 10-20% (je nach Artikel) |
Reduktion Standgebühren für Waggons | ca. 200'000 CHF pro Jahr |
Kunden | Â |
Servicegrad | 98% (+1%) |
Prozesse | Â |
Vereinfachte Zollabwicklung | durch Status „Bevorzugter Empfänger |
Transparenz | durch Zusammenführung aller prozessrelevanten Daten (via SAP ET 2000 und LAPS) |
Reduzierter Änderungsaufwand für Software | geringer, da Releasewechsel statt Eigenentwicklung |
Verbesserung Kommissionierleistung / Spitzenabdeckung | Erreicht durch Prozess-Reorganisation |
Reduktion Fehlerquote Kommissionierung | Geringer, da Kontrolle über Strichcode-Labels |
Mitarbeiter | Â |
Möglichkeit der persönlichen Weiterentwicklung | ![]() |
Aufbau von SAP Know-how für weitere Projekte | ![]() |
Innovation | Â |
Vereinfachte Abwicklung Privatkundenaufträge | ![]() |
Integration einer Handelsstufe | ![]() |
Â
Geplante Weiterentwicklungen
Das System läuft stabil, es ergeben sich jedoch ständig Weiterentwicklungsanforderungen, sei es aus internen Prozessverbesserungen, sei es durch Anforderungen von aussen. Monatliche Koordinationssitzungen einer Gruppe von 6 Fachbereichs- und 4 IT-Vertretern nehmen diese Anforderungen auf, entscheiden über ihre Umsetzung und treiben die weitere Verbesserung des Ersatzteilmanagements. Hohe Priorität hat dabei die ständige Verbesserung des Datenaustauschs mit VW. Nach dem Regionallager Luzern sollen nun sukzessive alle weiteren Regionallager organisatorisch und systemtechnisch in das Zentrallager integriert werden. Allerdings ist dieser Roll-out momentan (März 2002-März 2003) unterbrochen durch den Release-Wechsel des SAP ET zugrundeliegenden SAP R/3-Systems auf 4.6C.
Ein hohes Potential sieht die AMAG in der Automatisierung der kompletten Lagerverwaltung. Sie bereitet die Einführung eines Hochregallagers konzeptionell vor. Das Lagerhaltungssystem LAPS kann diese Art der Lagerhaltung nicht unterstützen. Bei der Auswahl des neuen Lagerhaltungssystems wird ein entscheidender Faktor sein, ob das System in der Lage ist, bei einem Ausfall des SAP-Systems temporär den Betrieb aufrecht zu erhalten.
5. Erkenntnisse
Die AMAG kann durch die Umstellung auf ein prozessorientiertes Ersatzteilmanagement und dessen systemtechnische Unterstützung die wachsende Komplexität des Ersatzteilgeschäfts beherrschen. Die Integration der Regionallager eliminiert Doppelarbeit und reduziert Schnittstellen. Die systemtechnische Unterstützung erlaubt Zeiteinsparung und Fehlerreduktion durch die Automatisierung von Prozessschritten. Die erhöhte Transparenz des Ersatzteilgeschäfts erlaubt es schliesslich, den Servicegrad trotz komplexerer Rahmenbedingungen konstant zu halten.
Bezogen auf Kooperation liefert der AMAG Fall folgende Erkenntnisse:
- Die AMAG stellte die Prozesse im Ersatzteilgeschäft kundenorientiert um.
- Die Echtzeitverfügbarkeit von Daten über die Prozesse des Ersatzteilgeschäftes erlaubt mittelfristig, um eine Handelsstufe zu reduzieren. Damit kann der Servicegrad trotz steigender Komplexität des Ersatzteilgeschäfts auf hohem Niveau gehalten werden.
- Der Hauptlieferant beeinflusst die Organisation des Ersatzteilgeschäfts stark, da in der Automobilbranche derzeit die Hersteller ihre Händler und Importeure dominieren. Die AMAG orientierte insbesondere bei der Systemimplementierung stark am Hauptlieferanten VW.
- Die AMAG passte ihre Prozesse an das System an – und nicht umgekehrt. Die Releasefähigkeit der Software und damit die Minimierung des Umstellungsaufwands wurde höher bewertet als die Unterstützung von Spezialprozessen. Standardsoftware erfordert grundsätzlich das Abwägen einer wirtschaftlich sinnvollen Balance zwischen passgenauer Prozessunterstützung und Erhaltung der Releasefähigkeit.
[1] Die Porsche AG hat ebenfalls ein SAP System im Einsatz, das sich jedoch wesentlich von SAP ET 2000 unterscheidet.