Support for Delivery and Return of Empties Process at Feldschlösschen Getränke AG
Feldschlösschen Getränke AG is the largest producer of beverages and the leading beverage distributor in Switzerland. As part of the project described, the process for taking back empty containers from retailers and catering establishments such as hotels, restaurants, bars, etc. was successfully optimised and automated using a mobile solution. Process optimisation included the introduction of PDAs and mobile printers with an infrared interface and integration with the SAP R/3-ERP system. The project achieved a payback time of ten months.
Table of Contents
1. The company2. E-business strategy
3. Integration solution
Business view, management of empty containers, process view, PDAs, application view, technical view
4. Implementation
Project management, software implementation/programming
5. Operation
Maintenance, cost, benefits?, profitability
6. Success factors
1. The company
Background, products:
Feldschlösschen Getränke AG is based in Rheinfelden and was founded in 1876. It is the largest beverage producer and the leading beverage distribution company in Switzerland. In 2002 the company achieved a turnover of CHF 930 million. Its annual production is 4.2 million hectolitres. It produces eleven own-brand beer and mineral water products and cooperates with strategic partners for soft drinks and mineral waters.
The company employs just under 2,000 people at a number of locations throughout Switzerland and operates seven factories, 19 distribution centres that deliver to catering businesses, the retail and drinks trade, and a company subsidiary.
The Feldschlösschen Group has been a wholly-owned subsidiary of the Danish company Carlsberg Breweries since 1 July 2001.
Sector:
In Switzerland, the beer market has shrunk by 20%, or 700,000 hectolitres, over the last 13 years. Total consumption in the 2001/2002 was 4.1 million hectolitres. The Feldschlösschen Group has a market share of 43% and a 55% share of Swiss beer production.
The market for mineral water in Switzerland grew by 50%, to 2.9 million hectolitres, over the last 12 years. The Feldschlösschen Group has a 22% market share of Switzerland's 5 million hectolitres mineral water production.
The project described here discusses the precise distribution of beverages and, in particular, the procedures for taking back empty containers from catering and drinks businesses (B2B). Reusable packaging accounts for approximately 60% of packaging used. Deliveries to the major distributors' regional distribution centres are not included in this solution.
Corporate strategy:
The corporate strategy of Feldschlösschen Getränke AG includes the following:
- Development of the Carlsberg premium brand in Switzerland.
- Expanding the position of national beer brands and own-brand mineral waters.
- Continuation of regional beer brands.
- Support of the "self-produced beer" and "self-produced mineral water" core business through strategic leader brands.
2. E-business strategy
The position of E-Business in the corporate strategy:
The company's approach to E-Business is to achieve lean E-Business solutions
that deliver useful benefits to business partners.
Intra-company E-Business application fields:
The company already operates various E-Commerce systems, including communication with major retail customers via EDI (Electronic Data Interchange). These customers can submit orders and receive delivery notes and invoices electronically.
There is also an E-Shop for catering companies (sample page at: http://www.feldschloesschen.com/e-commerce/d/anmeldung.htm). Registered customers log on with a user ID and password and can order via the internet, check statistics and obtain delivery status information. The orders are then processed directly in SAP. Around 5% of business with the catering sector is currently conducted through the E-Shop, which is used by approximately 1,000 catering customers.
Another solution uses XLM for data transmission via the internet between Feldschlösschen and its customers.
No E-Procurement solution is currently used.
Partners:
ERP suppliers and other IT partners
Since 1 January 2000, SAP R/3 has been running on an IBM iSeries (formerly AS/400). The Carlsberg parent company also uses SAP R/3 as its standard ERP system.
For this project, PEAK Technologies (Schweiz) AG was responsible for consulting, the hardware procurement and the implementation and integration of the PDA solution. PEAK Technologies was appointed as a result of a standard tender and evaluation process. The core business of PEAK Technologies (Schweiz) AG is the development and integration of software and network solutions for production, retail and logistics companies.
Resource Informatik AG (Wollerau) was commissioned to implement data communications between SAP R/3 and the PDA application, the technical interface, and data processing in the R/3 system. The company is a long-standing provider of SAP programming services to Feldschlösschen Getränke AG and a partner of SAP (Switzerland) AG. It specialises in providing services to all business sectors involving mySAP Enterprise and the SAP industry solutions IS-Utility, IS-Retail, IS-Beverages and IS-Space & Defence.
On the hardware side, there is an outsourcing agreement with IBM Switzerland. This includes operational management of the iSeries hardware on which SAP R/3 is installed.
3. Integration solution
Business view:
A fleet of approximately 260 vehicles provides daily deliveries of the beverages. [Management of empty containers] Approximately 840,000 deliveries are made every year. Containers are invoiced to the customers in the form of a refundable deposit. Packaging is often in the form of reusable containers such as crates with empty bottles, casks etc. When deliveries are made, empty containers from previous deliveries are collected at the same time. An average of 3.5 empty items are collected during each delivery, which works out at 3 million items per year. There are 160 different types of container to manage, or 750 types if the different variants are taken into account. Every day, between nine and eleven tons of products are moved.
The previous manual process required the driver to categorise each returned item and enter it by hand on the delivery note. With cash customers, the driver had to calculate the value of the returns and deduct this from the total amount shown on the delivery note. At the end of the delivery run, the delivery notes were sorted and the number of empty containers entered manually into the SAP system, which then credited the customers with the value of the returns and entered them back into stock. The problems with this procedure were as follows:
- Data entry is costly in terms of time and personnel. 32 employees were involved in the administration of empties.
- Invoicing was delayed because valuable time was lost between the driver's return in the late afternoon and entering the returns in the system.
- Frequent mistakes occurred through illegible handwriting and typing errors.
The following goals were set for the automation and optimisation of the empties handling procedure:
- Reduction of manual data entry. Data should be entered at the point of collection.
- Reduction in the time between accepting the returns and invoicing.
- Clear and easy to understand for the customer
- A simple solution ("drivers are not nerds")
- Fail-safe
- Reduction of errors with resultant reduction in corrections and improvement in customer satisfaction.
Â
Before the drivers set off on their rounds, the data for the trip is prepared at the depot in SAP R/3 and made available in a central directory on the iSeries server. Each driver and each route has its own file.
Each driver has his own PDA and a portable printer. A transfer cradle (a PDA docking station) is provided in each depot. The PDAs are placed in the transfer cradle before departure; the route information is transferred to the PDA, which is also time-synchronized (duration approximately four seconds). The driver enters the mileage of his vehicle before setting off. The time is automatically recorded.
In addition, the delivery documents are printed at the depot in the same way as before. These perform the function of delivery note for the customer, work sheet for the driver, and a backup solution during the trip.
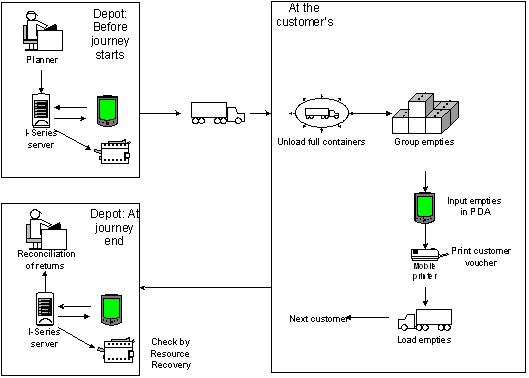
Fig. 3.1: Workflow
When the driver arrives at the customer's premises, he first unloads the delivery and then collects the empties. He then enters the details of the empties into the PDA. To identify the customer, the bar code on the delivery note is scanned into the PDA with its built-in bar code scanner. Alternatively, the driver can search for the customer's details manually in the PDA. Each collection of empties is thus allocated to a delivery note and a customer. Now, the returned items and quantities are entered. The driver can call up information about the returned items from his PDA.
When the details have been recorded, the PDA displays a summary of the items, which may then be corrected manually if required. The device also calculates the net amount due from cash customers - the value of the delivery, less credit for the empty returns.
Finally, the driver prints out a receipt on his portable printer for the empties he has collected and gives it to the customer. A second receipt is stapled to the delivery note, which the driver keeps. This procedure is repeated with each customer visited on the round.
At the end of the trip, the driver returns to the depot and records the mileage on his vehicle. The portable printer then prints out a daily report, which is spot-checked by the resource recovery department. The driver places the PDA back in the transfer cradle and transfers the data to the iSeries server. From there, the SAP system batch processes the data at 15-minute intervals and carries out a reconciliation of the returns. The data is now available for immediate invoicing.
The PDAs and portable printers are recharged at the depot overnight.
Application view:
The PDA application
An important requirement was that the PDA should be easy for the driver to understand and operate. The drivers sometimes have to work under poor lighting conditions. The software incorporates plausibility checks to ensure the quality of the recorded data. For example, a check is made whether the mileage entered at the end of the trip is greater than the mileage before departure. The start and finish times of the trip are recorded automatically. All information can be entered at the touch of a finger. Figures are entered using a large entry field on the Palm screen.
Completed deliveries are shown with a tick on the PDA screen. The PDA's software is multilingual, offering the driver a choice of German, French, Italian and English. Printouts can be made in the language the customer prefers.
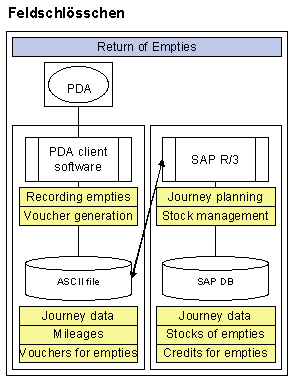
Figure 3.2: Integration of the mobile empties collection system at Feldschlösschen.
The software on the PDA includes the following functions:
- Download journey data
- Automatic installation of upgraded software when it becomes available
- Record mileage before departure
- Display a delivery overview
- Select customer (can be scanned in or entered manually)
- Display customer delivery header and delivery items
- Record empties items
- Calculation of net invoice amount (for cash customers)
- Printout of credit note for empties
- Record mileage before departure
- Generate and print out details of empties
- Upload data
Integration with SAP R/3
After finalising the journey schedule, the transportation planner prepares the order, delivery and transport data in ASCII format. This data is held in a SAP directory on the iSeries server for downloading before the start of the trip.
The data is uploaded at the end of the trip to the iSeries server.
A batch of ASCII data is sent to the SAP system every 15 minutes for processing. The data on the empties is added to the original customer order and the goods are booked in. The SAP system then conducts a number of plausibility checks. If they prove positive, the invoicing block is lifted and the order is released for invoicing. The transport data (kms driven and times) reported by the driver is then finalised.
The live data is thus stored only on the central computer. Local data backup is not necessary. The performance is problem-free, thanks to the very small amounts of data being transferred.
Technical view:
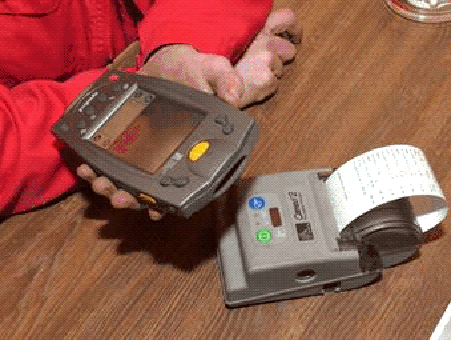
Figure 3.3: PDAs and portable printers
260 PDAs and portable printers are in service. The Symbol SPT-1700 was chosen as the PDA. These devices are equipped with the Palm OS platform, are very robust and suitable for an industrial environment (being dropped, subjected to heat, etc.). A bar code reader is built in. The PDA weighs 290 grammes and measures 17.8 x 9.2 x 2.5 cm.
The portable printer chosen is the Cameo 2 model made by Zebra. It communicates with the PDA via an infrared port. The device weighs 450 grammes and measures 16.7 x 9.4 x 6.6 cm. It is a thermal printer. The picture below shows both of these mobile units.
The diagram in Fig. 3.4 shows the network interface to the PDA with the SAP R/3 system. As already mentioned, the SAP system runs on an IBM iSeries (formerly AS/400) with the OS/400 operating system. The link operates as a batch job.
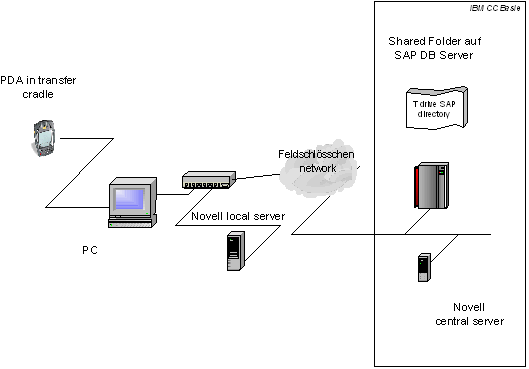
Figure 3.4: Integration of the PDA with SAP R/3
4. Implementation
Project management:
The project began in June 2001 with a preliminary study. Several process models were investigated with respect to feasibility, cost/benefit, complexity and stability. Based on the results of the preliminary study, a project proposal was presented to senior management and the decision was taken to go ahead with the project.
A pilot system was developed in the initial pilot phase between August and November 2001. Two drivers were involved in the project. As they gained experience with the system, they were able to contribute their own ideas. A decision was made to conduct a larger field study, based on the positive feedback from the pilot phase and the project's cost-effectiveness.
Rollout phase 1 lasted from January to May 2002, with a total of 100 devices in six locations. At first, five or six key users were trained at each location. Upon completion of their training, the key users were given the responsibility of training all of the other users. During a two-week period, both the old and the new systems were run in parallel.
The system was installed in the remaining locations in the second half of 2002 during phase 2 of the rollout. By the end of 2002, all 260 vehicles had been fitted with the system.
Mr. Senn of Feldschlösschen Getränke AG's computing department acted as project leader. PEAK Technologies (Schweiz) AG was responsible for the tendering and hardware acquisition
Software implementation / Programming:
The PDA application was developed by a programmer from PEAK Technologies (Schweiz) AG. The software runs on the Palm OS and was programmed using CodeWarrior. WinRFA was used as the transfer software. Because the software was developed to run under the Palm OS operating system, it can be used on any Palm OS device, and if necessary, will also be capable of running on different hardware in the future.
Resource Informatik AG carried out the integration with SAP R/3 using SAP IDoc and other applications.
5. Operation
Maintenance:
Feldschlösschen Getränke AG's computing department is providing support for the system. One person in each distribution centre, usually the coordinator, is responsible for the system. In addition, one person from Logistics provides 1st-level support for all of the centres and takes care of any problems that may arise.
New versions of the PDA application can be downloaded from the server. Any new version is automatically installed when the driver places the PDA in its transfer cradle in the morning. This solution works flawlessly and with a minimum of personnel.
Cost, benefits, profitability:
The investment costs were approximately three-quarters of a million Swiss francs. The project, based on a payback time of ten months, is also a financial success.
A particular benefit for the customer is that the data collected corresponds to what appears on the invoice. Mistakes due to poor handwriting or incorrect entries no longer occur, since 80% of all input is automated.
The driver is more than compensated for the small amount of extra effort by no longer having to spend large amounts of time keying in handwritten figures. Invoices can be produced and sent out promptly. Feldschlösschen Getränke AG now has at its disposal an effective controlling and analysis tool.
The project goals were met in full.
6. Success factors
Features of the solution:
Benefits
One of the most important factors contributing to the success of the project was simplicity. For example, no expensive middleware was needed. It was decided not to transfer the data to the centres by wireless radio (GSM) directly from the point of acquisition, since transferring the data to the ERP system at the end of the trip proved to be perfectly satisfactory.
Other success factors were the prior involvement in the project of its eventual users - especially the drivers and the schedulers - and the training of key users at their local distribution centres. Using a PDA gave the drivers greater job satisfaction and practically all of the drivers welcomed the solution. They particularly liked being able to produce an invoice on the spot with the PDA.
A side effect of the project is that the quarterly inventory can now be carried out with the same handheld devices. The inventory file is loaded onto the PDAs, the items are entered, and then transferred to SAP R/3. It is no longer necessary to enter information retrospectively from handwritten notes, with all the associated time, cost and mistakes. It took only 14 days to implement this additional function.
Problems
The drivers found operating the devices something of a challenge at first. Their colleagues in the back office were concerned about losing the manual entry system. Because of this, a rigorous check was kept on the system, which had a positive impact on system quality. In the meantime, those involved with the new system developed greater confidence and began to appreciate its usefulness and purpose.
The integration of the different operating systems (in particular OS 400 on the iSeries server and the Palm OS on the PDA) proved to be a problem that had to be resolved during the project.
One problem initially arose at the smaller distribution centres. During the test phase, tests had been carried out exclusively at locations with fast network connections. However, there were also other centres equipped with lower quality networks. At these, the PDAs would mistakenly transmit the data twice due to delays in the network. As a result, the data was duplicated and would be incorrectly processed in SAP. This problem has since been corrected.
The next steps
It is planned to add more functions to the PDAs. In future, the PDAs will also be able to deal with returned goods, faulty goods, customer enquiries and orders.
Lessons learned:
The results of this project are so positive that Feldschlösschen Getränke AG would not hesitate to repeat the project. Its implementation can be considered a total success.
The approach taken during the project has proven itself to be correct, as has the choice of project partners. The procedures for collecting the empties were optimized and automated as planned. The training activities, especially the involvement of key users at their local centres, seem to have made an important contribution to the project's success.
Despite all the planning, some problems only came to light after the system was already in operation. More care could have been taken to avoid the duplication of data in the SAP system. The key insight is that the major success factor of the project was its simplicity.